A method for solving the corrosion of high manganese thermoforming steel after pickling
A hot-forming steel and hot-forming technology, applied in metal rolling and other directions, can solve problems such as corrosion, high price, damage to surface finish and processing accuracy, and achieve the effect of reducing pickling time, simple method, and preventing corrosion
- Summary
- Abstract
- Description
- Claims
- Application Information
AI Technical Summary
Problems solved by technology
Method used
Image
Examples
Embodiment 1
[0041] A method for solving the corrosion of high manganese thermoforming steel after pickling:
[0042] Place the slab of high manganese hot-formed steel in a heating furnace and heat it to 1200°C at a rate of 45°C / min, stay at this temperature for 30 minutes, and the residual oxygen content in the heating furnace is ≤3%; heat the heated slab Rough rolling, a high-pressure nozzle is installed at the exit of the rough rolling mill. The shape of the nozzle of the high-pressure nozzle is flat oval, and the spray angle of the high-pressure nozzle is 30°. Enter the finish rolling mill, the inlet temperature of the finish rolling mill is 1010°C, start the double-pass descaling of the finish rolling mill, the rolling speed of the finish rolling mill is 8m / s, coil after finish rolling, the coiling temperature is 490°C, and the coiling temperature is 490°C, at 12°C / min The uncoiled slab enters the tension leveler, the bending roll insertion depth of the tension leveler is controlled a...
Embodiment 2
[0044] A method for solving the corrosion of high manganese thermoforming steel after pickling:
[0045] Place the slab of high manganese hot-formed steel in a heating furnace and heat it to 1180°C at a rate of 50°C / min, stay at this temperature for 35min, and the residual oxygen content in the heating furnace is ≤3%; Rough rolling, a high-pressure nozzle is installed at the exit of the rough rolling mill. The shape of the nozzle of the high-pressure nozzle is flat oval, and the spray angle of the high-pressure nozzle is 35°. Enter the finish rolling mill, the entrance temperature of the finish rolling mill is 1010°C, start the double pass descaling of the finish rolling mill, the rolling speed of the finish rolling mill is 8m / s, coil after finish rolling, the coiling temperature is 485°C, and the coiling temperature is 485°C, at 10°C / min The speed of cooling down to 60 ℃ is uncoiled; the uncoiled slab enters the tension leveler, and the insertion depth of the bending roll of ...
Embodiment 3
[0047] A method for solving the corrosion of high manganese thermoforming steel after pickling:
[0048] Place the slab of high manganese hot-formed steel in a heating furnace and heat it to 1210°C at a rate of 40°C / min, stay at this temperature for 25min, and the residual oxygen content in the heating furnace is ≤3%; Rough rolling, a high-pressure nozzle is installed at the exit of the rough rolling mill. The shape of the nozzle of the high-pressure nozzle is flat oval, and the spray angle of the high-pressure nozzle is 45°. Enter the finish rolling mill, the entrance temperature of the finish rolling mill is 1000°C, start the double-pass descaling of the finish rolling mill, the rolling speed of the finish rolling mill is 10m / s, coil after finish rolling, the coiling temperature is 480°C, and the coiling temperature is 480°C, at 15°C / min The speed of cooling down to 55 ℃ is uncoiled; the uncoiled slab enters the tension leveler, the bending roller insertion depth of the tens...
PUM
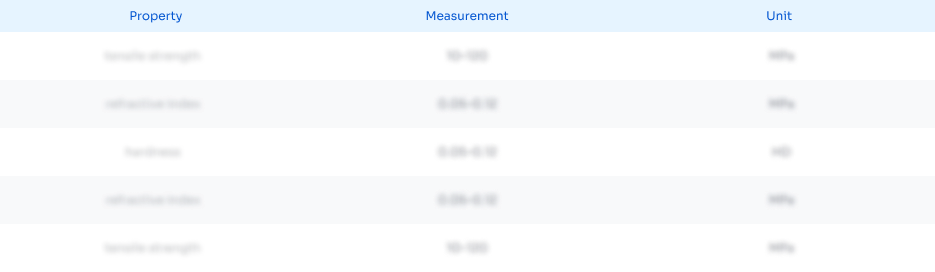
Abstract
Description
Claims
Application Information

- R&D
- Intellectual Property
- Life Sciences
- Materials
- Tech Scout
- Unparalleled Data Quality
- Higher Quality Content
- 60% Fewer Hallucinations
Browse by: Latest US Patents, China's latest patents, Technical Efficacy Thesaurus, Application Domain, Technology Topic, Popular Technical Reports.
© 2025 PatSnap. All rights reserved.Legal|Privacy policy|Modern Slavery Act Transparency Statement|Sitemap|About US| Contact US: help@patsnap.com