Textile fabric printing and dyeing and stacking device and method thereof
A technology for textile fabrics and equipment, which is applied in the field of textile fabric printing and dyeing lamination equipment, can solve the problems of pigment waste, limited dosage, and reduce the appearance quality of finished textile fabrics, and achieve the effect of improving the appearance quality
- Summary
- Abstract
- Description
- Claims
- Application Information
AI Technical Summary
Problems solved by technology
Method used
Image
Examples
Embodiment 1
[0045] Example one: such as Figure 3-11 As shown, a textile fabric printing and dyeing stacking equipment includes a workbench 1, a right platform 2, a printing and dyeing device 3, and a left platform 4 arranged on the workbench 1 and arranged from right to left. The bottom of the workbench 1 is welded There are multiple support legs 43 supported on the ground. The right platform 2 is provided with an unwinding mechanism 5, a softening device 6 and a leveling device 7 from right to left. The softening device 6 includes an air outlet 8 and fixed on the right platform 2 on the frame 9, the air outlet 8 is fixed on the frame 9, the air outlet of the air outlet 8 is set downwards, and the leveling device 7 includes a first gantry 10, a first cylinder 11, a first bracket 12, and The pressure roller 13 and the lower pressure roller 14, the first gantry 10 is fixed on the right platform 2, the first cylinder 11 is fixed on the beam of the first gantry 10, and the piston rod of the fi...
Embodiment 2
[0060] Embodiment two: such as Picture 12 As shown, a textile fabric printing and dyeing laminating equipment, the difference between this embodiment and the first embodiment is: the printing and dyeing laminating equipment also includes a PLC controller 45, the PLC controller 45 is arranged on the support leg 43, PLC control The installation position of the device 45 is just at the height that the workers can operate, so as to facilitate the workers to operate on the PLC controller 45. The PLC controller 45 is connected to the swing motor A19, the swing motor B32, the drive motor 26, and the electromagnetic of the vertical cylinder 35. The valve, the solenoid valve of the first cylinder 11 and the solenoid valve of the second cylinder 23 are electrically connected. The worker can control the activation or deactivation of the swing motor A19, the swing motor B32, and the drive motor 26 through the PLC controller 45, and can also control the first The extension or retraction of ...
PUM
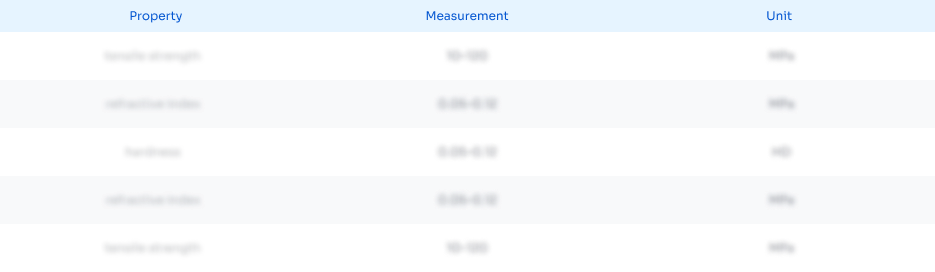
Abstract
Description
Claims
Application Information

- Generate Ideas
- Intellectual Property
- Life Sciences
- Materials
- Tech Scout
- Unparalleled Data Quality
- Higher Quality Content
- 60% Fewer Hallucinations
Browse by: Latest US Patents, China's latest patents, Technical Efficacy Thesaurus, Application Domain, Technology Topic, Popular Technical Reports.
© 2025 PatSnap. All rights reserved.Legal|Privacy policy|Modern Slavery Act Transparency Statement|Sitemap|About US| Contact US: help@patsnap.com