Multi-parameter sensing cutting tool wear monitoring method
A cutting tool and multi-parameter technology, which is applied in the direction of manufacturing tools, measuring/indicating equipment, metal processing machinery parts, etc., can solve the problems of inability to monitor tool wear in real time, limited precision, and cumbersome post-processing procedures of characteristic signals, etc., to promote Tool life and cutting production efficiency, promoting comprehensive improvement, and realizing the effect of intelligence
- Summary
- Abstract
- Description
- Claims
- Application Information
AI Technical Summary
Problems solved by technology
Method used
Image
Examples
Embodiment
[0012] A multi-parameter sensing cutting tool wear monitoring method, which monitors the cutting power by measuring the input current of the machine tool, the cutting force by the piezoelectric crystal dynamometer, the cutting vibration by the acceleration sensor, and the cutting temperature by the thermocouple and the infrared thermal imager , to obtain the system monitoring feature signal; the method of gray system theory is used to fit the multi-parameter perception equation of the flank wear of the tool about the monitoring feature signal and cutting parameters; the solution program of the integrated perception equation is constructed by using LabVIEW software, through The programmed automatic solution of the perception equation realizes the real-time monitoring of cutting tool wear.
PUM
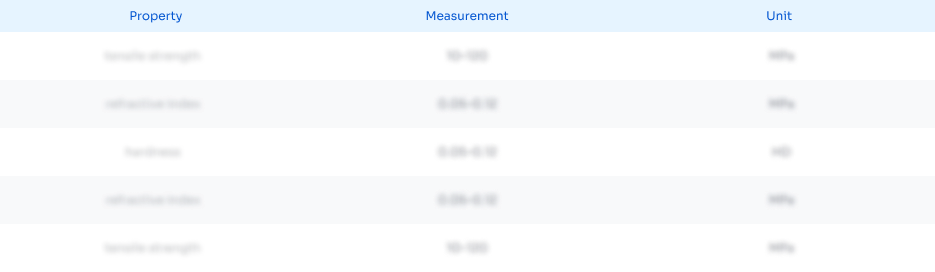
Abstract
Description
Claims
Application Information

- Generate Ideas
- Intellectual Property
- Life Sciences
- Materials
- Tech Scout
- Unparalleled Data Quality
- Higher Quality Content
- 60% Fewer Hallucinations
Browse by: Latest US Patents, China's latest patents, Technical Efficacy Thesaurus, Application Domain, Technology Topic, Popular Technical Reports.
© 2025 PatSnap. All rights reserved.Legal|Privacy policy|Modern Slavery Act Transparency Statement|Sitemap|About US| Contact US: help@patsnap.com