Digital controlled lathe thermal error measuring compensation system and method
A technology of CNC lathe and compensation system, applied in the field of CNC machine tools
- Summary
- Abstract
- Description
- Claims
- Application Information
AI Technical Summary
Problems solved by technology
Method used
Image
Examples
Embodiment Construction
[0064] The present invention will be further described in detail below in conjunction with the accompanying drawings and specific implementation.
[0065] Such as figure 1 , figure 2 As shown, a thermal error measurement and compensation system for a CNC lathe includes an eddy current displacement sensor 9, a platinum resistance temperature sensor 1, a laser interferometer, a displacement acquisition and processing module, a thermal error compensation module and a PC, wherein the eddy current displacement sensor 9 and The displacement acquisition and processing module is connected and transmits the real-time measured spindle rod 10 and tool position information. The displacement acquisition and processing module is connected to the PC through the serial port, and the laser interferometer is connected to the PC to measure the positioning error of the measuring point of the feed system. Platinum The resistance temperature sensor 1 is connected with the thermal error compensati...
PUM
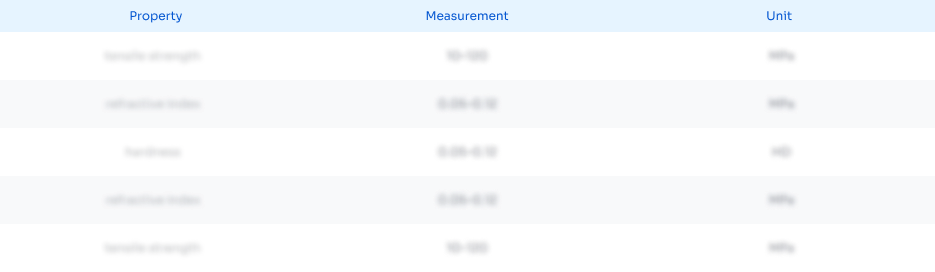
Abstract
Description
Claims
Application Information

- R&D
- Intellectual Property
- Life Sciences
- Materials
- Tech Scout
- Unparalleled Data Quality
- Higher Quality Content
- 60% Fewer Hallucinations
Browse by: Latest US Patents, China's latest patents, Technical Efficacy Thesaurus, Application Domain, Technology Topic, Popular Technical Reports.
© 2025 PatSnap. All rights reserved.Legal|Privacy policy|Modern Slavery Act Transparency Statement|Sitemap|About US| Contact US: help@patsnap.com