Preparation method of silicon dioxide aerogel thermal insulation filler
A technology of silica and thermal insulation fillers, applied in chemical instruments and methods, fibrous fillers, inorganic pigment treatment, etc., can solve the problems of reduction, micropores are easily blocked, thermal insulation performance, etc., and achieve simple production process and good thermal insulation performance. Effect
- Summary
- Abstract
- Description
- Claims
- Application Information
AI Technical Summary
Problems solved by technology
Method used
Image
Examples
Embodiment 1
[0026] (1). Dissolve 1 kg of inorganic foaming agent ammonium bicarbonate in 20 kg of water, then add 10 kg of silica airgel, stir and mix evenly, so that the inorganic foaming agent is fully filled into the micropores of silica airgel , filter to remove excess liquid, pre-block the pores, and obtain non-porous silica airgel;
[0027] (2). Add 1kg of paraffin wax to a reaction kettle at 70°C, heat and melt, add 0.5kg of calcium chloride and grind it evenly, spray it on the surface of 30kg of non-porous silica airgel prepared in step (1), and then add it to Stir in 120kg of water, add 1kg of HTK-5040 to completely disperse the paraffin-coated silica airgel in water to obtain a dispersion system;
[0028] (3). Add sodium carbonate to the dispersion system described in (2) to obtain a saturated solution, and stir until the calcium chloride and sodium carbonate in the paraffin coated on the surface of the silica airgel form a calcium carbonate coating layer, centrifugally filtere...
Embodiment 2
[0030](1). Dissolve 2kg of inorganic foaming agent ammonium bicarbonate in 20kg of water, then add 12kg of silica airgel, stir and mix evenly, so that the inorganic foaming agent is fully filled into the micropores of silica airgel , filter to remove excess liquid, pre-block the pores, and obtain non-porous silica airgel;
[0031] (2). Add 1kg of paraffin wax to a reaction kettle at 70°C, heat and melt, add 1kg of calcium chloride and grind it evenly, spray it on the surface of 32kg of non-porous silica airgel prepared in step (1), and then add it to 150kg Stir in water, add 1kg of HTK-5040 to completely disperse the paraffin-coated silica airgel in water to obtain a dispersion system;
[0032] (3). Add sodium carbonate to the dispersion system described in (2) to obtain a saturated solution, and stir until the calcium chloride and sodium carbonate in the paraffin coated on the surface of the silica airgel form a calcium carbonate coating layer, centrifuged and dried at 80°C ...
Embodiment 3
[0034] (1). Dissolve 1.5kg of inorganic foaming agent ammonium bicarbonate in 20kg of water, then add 15kg of silica airgel, stir and mix evenly, so that the inorganic foaming agent can be fully filled into the microspheres of silica airgel In the pores, the excess liquid is removed by filtration, and the pores are pre-blocked to obtain non-porous silica airgel;
[0035] (2). Add 1kg of paraffin wax to a reaction kettle at 60°C, heat and melt, add 0.5kg of calcium chloride and grind it evenly, spray it on the surface of 35kg of non-porous silica airgel prepared in step (1), and then add it to Stir in 100kg of water, add 1kg of HTK-5040 to completely disperse the paraffin-coated silica airgel in water to obtain a dispersion system;
[0036] (3). Add sodium carbonate to the dispersion system described in (2) to obtain a saturated solution, and stir until the calcium chloride and sodium carbonate in the paraffin coated on the surface of the silica airgel form a calcium carbonate ...
PUM
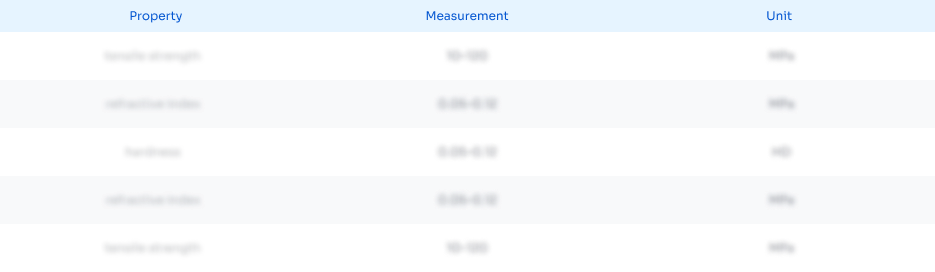
Abstract
Description
Claims
Application Information

- R&D Engineer
- R&D Manager
- IP Professional
- Industry Leading Data Capabilities
- Powerful AI technology
- Patent DNA Extraction
Browse by: Latest US Patents, China's latest patents, Technical Efficacy Thesaurus, Application Domain, Technology Topic, Popular Technical Reports.
© 2024 PatSnap. All rights reserved.Legal|Privacy policy|Modern Slavery Act Transparency Statement|Sitemap|About US| Contact US: help@patsnap.com