Temperature control system of hydraulic retarder
A temperature control system, hydraulic retarder technology, applied in the direction of liquid resistance brakes, magnetic drive clutches, clutches, etc., can solve the asymmetry of heat dissipation capacity, can not bypass the temperature control, and the heat dissipation capacity of the water tank can not solve the hydraulic retardation To solve problems such as heat of the controller, achieve the effect of smooth torque output curve, reduce excessive attention, and shorten training time
- Summary
- Abstract
- Description
- Claims
- Application Information
AI Technical Summary
Problems solved by technology
Method used
Image
Examples
Embodiment Construction
[0019] The following will clearly and completely describe the technical solutions in the embodiments of the present invention with reference to the accompanying drawings in the embodiments of the present invention. Obviously, the described embodiments are only some of the embodiments of the present invention, not all of them.
[0020] Since the heat dissipation system of the hydraulic retarder must be connected in series with the engine heat dissipation system, the problems are as follows: 1. The engine speed is required to be no less than 1800 rpm under working conditions; the working temperature must not reach or exceed 160 degrees Celsius, which distracts the driver's attention force.
[0021] 2. Due to the working conditions of the engine and the nature of heat exchange between oil and water, it runs at high temperature for a long time and its parameters and performance boundaries, resulting in insufficient torque and damage to the body.
[0022] 3. The pipelines of the en...
PUM
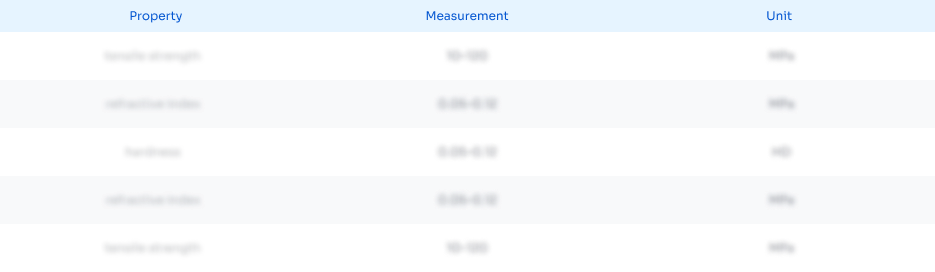
Abstract
Description
Claims
Application Information

- R&D Engineer
- R&D Manager
- IP Professional
- Industry Leading Data Capabilities
- Powerful AI technology
- Patent DNA Extraction
Browse by: Latest US Patents, China's latest patents, Technical Efficacy Thesaurus, Application Domain, Technology Topic, Popular Technical Reports.
© 2024 PatSnap. All rights reserved.Legal|Privacy policy|Modern Slavery Act Transparency Statement|Sitemap|About US| Contact US: help@patsnap.com