Preparation method of high-water-flux high-toughness nanofiltration membrane
A high-toughness, nanofiltration membrane technology, applied in the field of separation membranes, can solve problems such as insufficient water flux, low water flux, and insufficient hydrophilicity of nanofiltration membranes.
- Summary
- Abstract
- Description
- Claims
- Application Information
AI Technical Summary
Problems solved by technology
Method used
Examples
Embodiment 1
[0030] Preparation of enzymatic hydrolyzate:
[0031] Throw graphite flakes and sulfuric acid solution with a mass fraction of 80% into a beaker at a mass ratio of 1:10, place the beaker in a water bath with a water bath temperature of 0°C, and stir with a stirrer at a speed of 120r / min for 40min. Reaction slurry, adding potassium ferrate powder with a mass of 1.0% of the reaction slurry to the reaction slurry, raising the temperature of the water bath to 20°C, stirring and mixing for 30 minutes to obtain an oxidation reaction solution;
[0032] Put the above oxidation reaction solution into a suction filter to obtain filter residue, wash the filter residue 3 times with distilled water to obtain an oxidation product, put the oxidation product and cotton into a pulverizer at a mass ratio of 5:1 and mix them to obtain a mixture. The mixture and cellulase are put into the enzymolysis tank at a mass ratio of 200:1, and the enzymolysis tank is placed in a greenhouse at an indoor te...
Embodiment 2
[0040] Preparation of enzymatic hydrolyzate:
[0041] Put flake graphite and sulfuric acid solution with a mass fraction of 85% into a beaker at a mass ratio of 1:10, place the beaker in a water bath with a water bath temperature of 2°C, and stir with a stirrer at a speed of 140r / min for 50min. Reaction slurry, adding potassium ferrate powder with a mass of 1.2% of the reaction slurry to the reaction slurry, raising the temperature of the water bath to 25°C, stirring and mixing for 35 minutes to obtain an oxidation reaction solution;
[0042] Put the above oxidation reaction solution into a suction filter and filter to obtain the filter residue, wash the filter residue with distilled water 4 times to obtain the oxidation product, put the oxidation product and cotton into the pulverizer at a mass ratio of 5:1 and mix them to obtain a mixture. The mixture and cellulase are put into the enzymolysis tank at a mass ratio of 200:1, and the enzymolysis tank is placed in a greenhouse ...
Embodiment 3
[0050] Preparation of enzymatic hydrolyzate:
[0051] Put flake graphite and sulfuric acid solution with a mass fraction of 90% into a beaker at a mass ratio of 1:10, place the beaker in a water bath with a water bath temperature of 5°C, and stir with a stirrer at a speed of 150r / min for 60min. Reaction slurry, adding potassium ferrate powder with a mass of 1.5% of the reaction slurry to the reaction slurry, raising the temperature of the water bath to 30°C, stirring and mixing for 40 minutes to obtain an oxidation reaction solution;
[0052] Put the above oxidation reaction solution into a suction filter and filter to obtain the filter residue, wash the filter residue with distilled water for 5 times to obtain the oxidation product, put the oxidation product and cotton into the pulverizer at a mass ratio of 5:1 and mix them to obtain a mixture. The mixture and cellulase are put into the enzymolysis tank at a mass ratio of 200:1, and the enzymolysis tank is placed in a greenho...
PUM
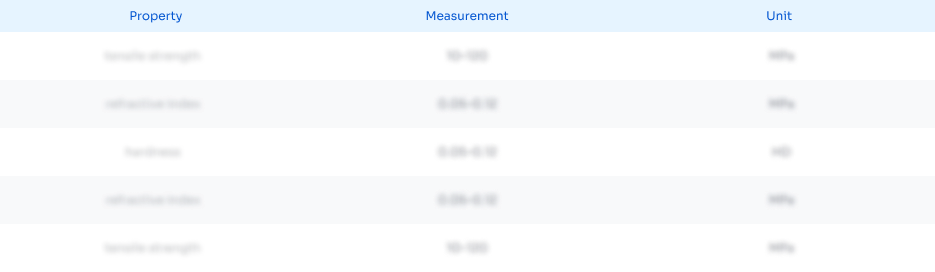
Abstract
Description
Claims
Application Information

- R&D
- Intellectual Property
- Life Sciences
- Materials
- Tech Scout
- Unparalleled Data Quality
- Higher Quality Content
- 60% Fewer Hallucinations
Browse by: Latest US Patents, China's latest patents, Technical Efficacy Thesaurus, Application Domain, Technology Topic, Popular Technical Reports.
© 2025 PatSnap. All rights reserved.Legal|Privacy policy|Modern Slavery Act Transparency Statement|Sitemap|About US| Contact US: help@patsnap.com