A kind of preparation method and application of graphene powder
A technology of graphene powder and graphite powder, which is applied in the field of graphene powder preparation, can solve the problems of not meeting the demand for graphene powder materials, high equipment cost requirements, and large consumption of chemical reagents, and achieve good electronic conductivity and Effect of load transfer, reduction of application cost, effect of low application cost
- Summary
- Abstract
- Description
- Claims
- Application Information
AI Technical Summary
Problems solved by technology
Method used
Image
Examples
Embodiment 1
[0031] This embodiment includes the following steps:
[0032] Step 1. Pretreatment: Add 500g of commercially available flake graphite powder to 1000mL of acetone, use 50kW power to ultrasonically clean for 50min to remove surface oil and impurities, then stand until stratified, pour out the supernatant liquid, and pour out the graphite powder on the lower layer Add ethanol to the colloid for cleaning, and then vacuum freeze-dry for 15 hours at a vacuum degree of -0.1MPa and a temperature of -80°C to obtain pretreated graphite powder;
[0033] Step 2, intercalation heat treatment: the pretreated graphite powder obtained in step 1 is protected by a hydrogen-argon mixed atmosphere and subjected to an intercalation heat treatment at a temperature of 800°C for 6 hours; the volume ratio of hydrogen to argon in the hydrogen-argon mixed atmosphere 4:1, the flow rate of hydrogen-argon mixed atmosphere is 2L / min;
[0034]Step 3, ball milling and exfoliation treatment: the graphite powd...
Embodiment 2
[0040] This embodiment includes the following steps:
[0041] Step 1. Pretreatment: Add 10g of commercially available flake graphite powder into 100mL of acetone, use 30kW power to ultrasonically clean for 30min to remove surface oil and impurities, then let stand until stratified, pour out the supernatant liquid, and pour out the graphite powder on the lower layer Add ethanol to the colloid for cleaning, and then vacuum freeze-dry for 10 hours at a vacuum degree of -0.1MPa and a temperature of -80°C to obtain pretreated graphite powder;
[0042] Step 2, intercalation heat treatment: the pretreated graphite powder obtained in step 1 is protected by a hydrogen-argon mixed atmosphere and subjected to an intercalation heat treatment at a temperature of 600°C for 4 hours; the volume ratio of hydrogen to argon in the hydrogen-argon mixed atmosphere 4:1, the flow rate of hydrogen-argon mixed atmosphere is 10L / min;
[0043] Step 3, ball milling and exfoliation treatment: the graphit...
Embodiment 3
[0045] This embodiment includes the following steps:
[0046] Step 1. Pretreatment: Add 2000g of commercially available flake graphite powder to 2000mL of acetone, use 100kW power to ultrasonically clean for 60min to remove surface oil and impurities, then stand until stratified, pour out the supernatant liquid, and pour out the graphite powder on the lower layer Add ethanol to the colloid for cleaning, and then vacuum freeze-dry for 30 hours under the conditions of vacuum degree of -0.1MPa and temperature of -80°C to obtain pretreated graphite powder;
[0047] Step 2, intercalation heat treatment: the pretreated graphite powder obtained in step 1 is protected by a hydrogen-argon mixed atmosphere and subjected to an intercalation heat treatment at a temperature of 1000°C for 10 hours; the volume ratio of hydrogen to argon in the hydrogen-argon mixed atmosphere 4:1, the flow rate of hydrogen-argon mixed atmosphere is 5L / min;
[0048] Step 3, ball milling and exfoliation treatm...
PUM
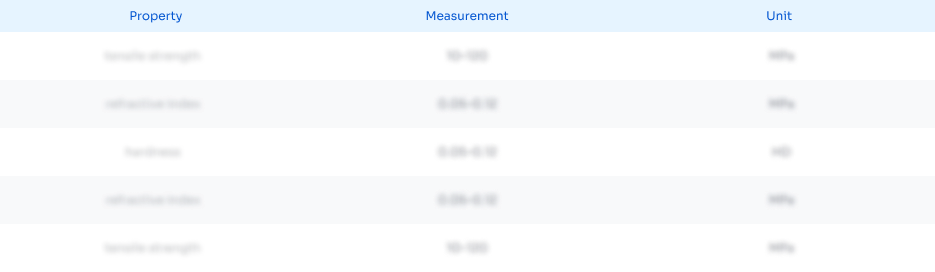
Abstract
Description
Claims
Application Information

- R&D
- Intellectual Property
- Life Sciences
- Materials
- Tech Scout
- Unparalleled Data Quality
- Higher Quality Content
- 60% Fewer Hallucinations
Browse by: Latest US Patents, China's latest patents, Technical Efficacy Thesaurus, Application Domain, Technology Topic, Popular Technical Reports.
© 2025 PatSnap. All rights reserved.Legal|Privacy policy|Modern Slavery Act Transparency Statement|Sitemap|About US| Contact US: help@patsnap.com