Preparation method of high-flux and high-strength polytetrafluoroethylene water body filtration composite nanofiltration membrane
A technology of polytetrafluoroethylene and composite nanofiltration membranes, which is applied in chemical instruments and methods, membranes, membrane technologies, etc., can solve the problems of basement membrane rupture and decrease in the strength of polytetrafluoroethylene basement membranes, and achieve control of reaction time, Improves water flux and avoids the effect of reducing infiltration efficiency
- Summary
- Abstract
- Description
- Claims
- Application Information
AI Technical Summary
Problems solved by technology
Method used
Image
Examples
Embodiment 1
[0027] A method for preparing a high-throughput and high-strength polytetrafluoroethylene composite nanofiltration membrane for water filtration, comprising the following steps:
[0028] S1. Hydrophilic modification treatment of hydrophobic PTFE microfiltration membrane:
[0029] Put the hydrophobic polytetrafluoroethylene microfiltration membrane into absolute ethanol for ultrasonic cleaning, dry, and set aside;
[0030] Add an aqueous solution of hydrochloric acid with a mass concentration of 10% into absolute ethanol at a ratio of 1:3 by volume, and stir evenly to obtain solution a. Add tetrabutyl titanate and nano silicon dioxide into absolute ethanol, tetratitanate The mass ratio of butyl ester to nano silicon dioxide is 1:0.4, the mass volume ratio of tetrabutyl titanate to absolute ethanol is 1g / 50mL, ultrasonic oscillation is carried out to obtain solution b, and the above-mentioned dried polytetrafluoroethylene micro Immerse the filter membrane in solution b, then sl...
Embodiment 2
[0037] A method for preparing a high-throughput and high-strength polytetrafluoroethylene composite nanofiltration membrane for water filtration, comprising the following steps:
[0038] S1. Hydrophilic modification treatment of hydrophobic PTFE microfiltration membrane:
[0039] Put the hydrophobic polytetrafluoroethylene microfiltration membrane into absolute ethanol for ultrasonic cleaning, dry, and set aside;
[0040] Add an aqueous solution of hydrochloric acid with a mass concentration of 10% into absolute ethanol at a ratio of 1:3 by volume, and stir evenly to obtain solution a. Add tetrabutyl titanate and nano silicon dioxide into absolute ethanol, tetratitanate The mass ratio of butyl ester to nano silicon dioxide is 1:0.3, the mass volume ratio of tetrabutyl titanate to absolute ethanol is 1g / 50mL, ultrasonic oscillation is carried out to obtain solution b, and the above-mentioned dried polytetrafluoroethylene micro Immerse the filter membrane in solution b, then sl...
Embodiment 3
[0047] A method for preparing a high-throughput and high-strength polytetrafluoroethylene composite nanofiltration membrane for water filtration, comprising the following steps:
[0048] S1. Hydrophilic modification treatment of hydrophobic PTFE microfiltration membrane:
[0049] Put the hydrophobic polytetrafluoroethylene microfiltration membrane into absolute ethanol for ultrasonic cleaning, dry, and set aside;
[0050] Add an aqueous solution of hydrochloric acid with a mass concentration of 10% into absolute ethanol at a ratio of 1:3 by volume, and stir evenly to obtain solution a. Add tetrabutyl titanate and nano silicon dioxide into absolute ethanol, tetratitanate The mass ratio of butyl ester to nano silicon dioxide is 1:0.5, the mass volume ratio of tetrabutyl titanate to absolute ethanol is 1g / 50mL, ultrasonic oscillation is carried out to obtain solution b, and the above-mentioned dried polytetrafluoroethylene micro Immerse the filter membrane in solution b, then sl...
PUM
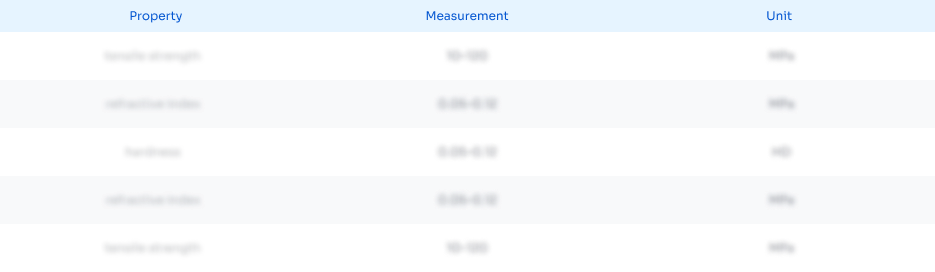
Abstract
Description
Claims
Application Information

- R&D
- Intellectual Property
- Life Sciences
- Materials
- Tech Scout
- Unparalleled Data Quality
- Higher Quality Content
- 60% Fewer Hallucinations
Browse by: Latest US Patents, China's latest patents, Technical Efficacy Thesaurus, Application Domain, Technology Topic, Popular Technical Reports.
© 2025 PatSnap. All rights reserved.Legal|Privacy policy|Modern Slavery Act Transparency Statement|Sitemap|About US| Contact US: help@patsnap.com