Preparing method of phenolic fibers
A technology of phenolic fiber and phenolic resin, which is applied in the field of melt spinning, can solve the problems of low efficiency of phenolic resin melt spinning process, long curing and crosslinking time, complicated preparation process, etc., and achieve stable and continuous spinning and high spinning efficiency High and uniform fiber fineness
- Summary
- Abstract
- Description
- Claims
- Application Information
AI Technical Summary
Problems solved by technology
Method used
Image
Examples
Embodiment 1
[0026] The phenolic resin with a mass fraction of 99% and 1% copolymerized nylon are uniformly mixed, and the mixed material enters the twin-screw extruder for melting and blending to form a melt, and then the melt enters the single-screw connected to the head of the twin-screw extruder Extruder, and then enter the spinning assembly through the metering pump, the pressure of the assembly is 0.1MPa, the ejected silk enters the aspirator at 0.5m below the outlet hole, the aspirating speed is 300m / min, and the silk is conveyed The pipeline is transported to the fiber collection device to obtain the phenolic fiber precursor.
[0027] Soak the phenolic fiber precursors at 5°C into a solidification solution with a mass content of 20% formaldehyde, 16% hydrochloric acid, and 64% deionized water, and stay for 15 minutes; heat up to 40°C at 2°C / min , stay for 10min; then raise the temperature to 60℃ at 2℃ / min, stay for 20min; then raise the temperature to 80℃ at 2℃ / min, stay for 20min;...
Embodiment 2
[0029]Mix the phenolic resin with a mass fraction of 85% and 15% copolymerized nylon evenly, and the mixed material enters the twin-screw extruder to melt and blend to form a melt, and then the melt enters the single-screw connected to the head of the twin-screw extruder Extruder, and then enter the spinning assembly through the metering pump, the assembly pressure is 1.5MPa, the ejected silk enters the silk suction device at 1m below the silk outlet hole, the suction speed is 800m / min, and passes through the silk pipeline Transport to the collection device to obtain phenolic fiber precursors.
[0030] Soak the phenolic fiber precursors at 30°C in a solidification solution with a mass content of 20% formaldehyde, 16% hydrochloric acid, and 64% water, and stay for 30 minutes; heat up to 40°C at 2°C / min, and stay 10min; then heat up to 60°C at 2°C / min and stay for 20min; then heat up to 80°C at 2°C / min and stay for 20min; continue to heat up to boiling at 3°C / min and stay for 30...
Embodiment 3
[0032] Mix the phenolic resin with a mass fraction of 90% and 10% copolymerized nylon evenly, and the mixed material enters the twin-screw extruder to melt and blend to form a melt, and then the melt enters the single-screw connected to the head of the twin-screw extruder Extruder, and then enter the spinning assembly through the metering pump, the assembly pressure is 1.2MPa, the ejected silk enters the silk suction device at 1m below the silk outlet hole, the suction speed is 1800m / min, and passes through the silk delivery pipeline Transport to the collection device to obtain phenolic fiber precursors.
[0033] Soak the phenolic fiber precursors at 15°C into a solidification solution with a mass content of 20% formaldehyde, 16% hydrochloric acid, and 64% water, and stay for 30 minutes; heat up to 40°C at 3°C / min, and stay 10min; then heat up to 60°C at 3°C / min and stay for 20min; then heat up to 80°C at 3°C / min and stay for 20min; continue to heat up to boiling at 3°C / min an...
PUM
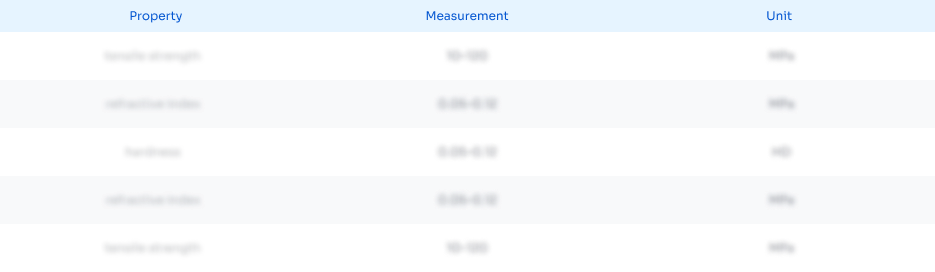
Abstract
Description
Claims
Application Information

- R&D
- Intellectual Property
- Life Sciences
- Materials
- Tech Scout
- Unparalleled Data Quality
- Higher Quality Content
- 60% Fewer Hallucinations
Browse by: Latest US Patents, China's latest patents, Technical Efficacy Thesaurus, Application Domain, Technology Topic, Popular Technical Reports.
© 2025 PatSnap. All rights reserved.Legal|Privacy policy|Modern Slavery Act Transparency Statement|Sitemap|About US| Contact US: help@patsnap.com