High-conductivity copper alloy rotor and preparation method thereof
A copper alloy, high electrical conductivity technology, applied in the field of high electrical conductivity copper alloy rotor and its preparation, can solve the problems of poor electrical conductivity, easy wear and service life, and achieve the effects of improving electrical conductivity, increasing strength, and reducing production costs
- Summary
- Abstract
- Description
- Claims
- Application Information
AI Technical Summary
Problems solved by technology
Method used
Examples
Embodiment 1
[0023] A high-conductivity copper alloy rotor comprises the following raw materials in weight percentage: 0.1% of chromium, 0.1% of zirconium, 0.02% of lithium, 0.02% of manganese and 0.01% of lanthanum, and the balance is copper.
[0024] The preparation method of the above-mentioned high-conductivity copper alloy rotor comprises the following steps:
[0025] (1) Put copper in a vacuum induction melting furnace, keep it warm at 1100°C for 5 minutes, then add copper-10wt% chromium master alloy, copper-10wt% zirconium master alloy, copper-10wt% lithium master alloy, BMn40-1.5 For the manganese-copper alloy, heat it up to 1250°C for 10 minutes, then add Cu20La copper-lanthanum master alloy, keep the temperature constant, and keep it for 5 minutes to obtain a copper alloy smelting solution;
[0026] (2) Die-cast the copper alloy smelting solution obtained in step (1) under a pressure of 70 MPa, then heat it at 800° C. for 20 minutes, and cool it to room temperature to obtain a ca...
Embodiment 2
[0029] A high-conductivity copper alloy rotor comprises the following raw materials in weight percentage: 0.9% of chromium, 0.2% of zirconium, 0.02% of lithium, 0.02% of manganese and 0.02% of cerium, and the balance is copper.
[0030] The preparation method of the above-mentioned high-conductivity copper alloy rotor comprises the following steps:
[0031] (1) Put copper in a vacuum induction melting furnace, keep it warm at 1150°C for 8 minutes, then add copper-10wt% chromium master alloy, copper-10wt% zirconium master alloy, copper-10wt% lithium master alloy, BMn40-1.5 For the manganese-copper alloy, heat it up to 1300°C for 20 minutes, and finally add Cu20Ce copper-cerium intermediate alloy, keep the temperature constant, and keep it for 8 minutes again to obtain a copper alloy smelting solution;
[0032] (2) Die-cast the copper alloy smelting solution obtained in step (1) under a pressure of 75 MPa, then heat it at 850° C. for 30 minutes, and cool it to room temperature t...
Embodiment 3
[0035] A high-conductivity copper alloy rotor, including the following raw materials in weight percentage: 1.2% chromium, 0.3% zirconium, 0.02% lithium, 0.02% manganese and 0.03% rare earth metal (lanthanum and cerium are mixed in a mass ratio of 1:1), and the balance is copper.
[0036] The preparation method of the above-mentioned high-conductivity copper alloy rotor comprises the following steps:
[0037] (1) Put copper in a vacuum induction melting furnace, keep it warm at 1200°C for 10 minutes, then add copper-10wt% chromium master alloy, copper-10wt% zirconium master alloy, copper-10wt% lithium master alloy, BMn40-1.5 For the manganese-copper alloy, heat it up to 1300°C for 25 minutes, and finally add Cu20La copper-lanthanum master alloy and Cu20Ce copper-cerium master alloy, keep the temperature constant, and keep the temperature for 8 minutes again to obtain a copper alloy smelting solution;
[0038] (2) Die-cast the copper alloy smelting solution obtained in step (1)...
PUM
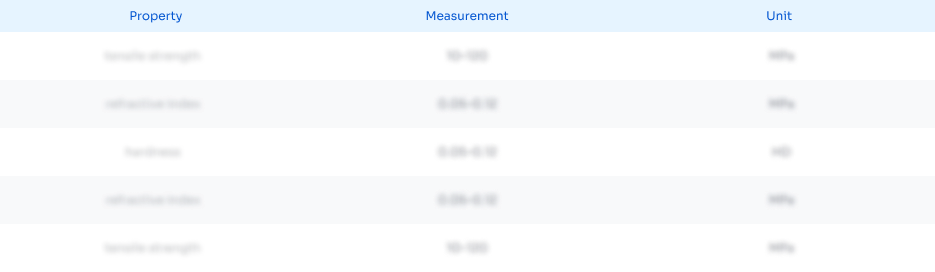
Abstract
Description
Claims
Application Information

- R&D Engineer
- R&D Manager
- IP Professional
- Industry Leading Data Capabilities
- Powerful AI technology
- Patent DNA Extraction
Browse by: Latest US Patents, China's latest patents, Technical Efficacy Thesaurus, Application Domain, Technology Topic, Popular Technical Reports.
© 2024 PatSnap. All rights reserved.Legal|Privacy policy|Modern Slavery Act Transparency Statement|Sitemap|About US| Contact US: help@patsnap.com