Laminating process of aluminum substrate
A lamination process and aluminum substrate technology, applied in lamination, lamination devices, layered products, etc., can solve problems affecting production efficiency, time-consuming, long completion time, etc., to improve board-forming efficiency and save time Effect
- Summary
- Abstract
- Description
- Claims
- Application Information
AI Technical Summary
Problems solved by technology
Method used
Image
Examples
Embodiment Construction
[0023] The present invention will be described in further detail below in conjunction with the accompanying drawings.
[0024] Such as figure 1 As shown, this embodiment includes the following steps,
[0025] The positioning hole processing step is to process the positioning slot holes on the prepreg 2 and the substrate 3;
[0026] Etching step, the substrate 3 is etched;
[0027] The stacking step is to stack the plates in the carrier tray to form the primary plate body;
[0028] Heating step, copper foil 1, prepreg 2 and substrate 3 such as figure 2 The primary plates stacked in sequence as shown are heated to a rated high temperature until the prepreg 2 is heated to a liquid state;
[0029] Lamination step, using a laminator to laminate the primary board body at a high temperature rating;
[0030] In the cooling step, the primary plate body in lamination is cooled to a rated low temperature to form a secondary plate body, and the primary plate body is cooled to a rate...
PUM
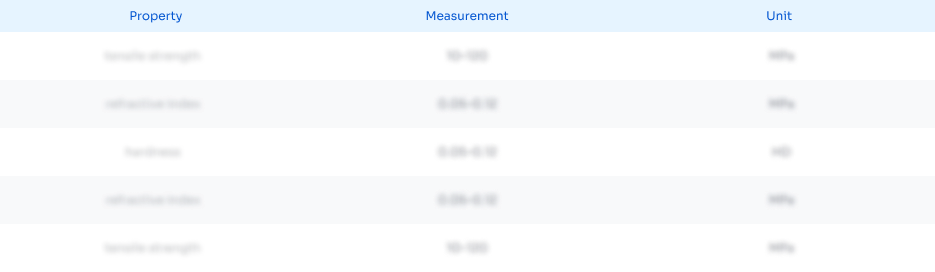
Abstract
Description
Claims
Application Information

- R&D
- Intellectual Property
- Life Sciences
- Materials
- Tech Scout
- Unparalleled Data Quality
- Higher Quality Content
- 60% Fewer Hallucinations
Browse by: Latest US Patents, China's latest patents, Technical Efficacy Thesaurus, Application Domain, Technology Topic, Popular Technical Reports.
© 2025 PatSnap. All rights reserved.Legal|Privacy policy|Modern Slavery Act Transparency Statement|Sitemap|About US| Contact US: help@patsnap.com