Method for preparing corrosion pit in metal material sample
A metal material and corrosion pit technology, which is applied in the field of metal material sample pretreatment, can solve the problems of long preparation period of corrosion pit and the lack of general applicability of the preparation method to metal materials, and achieves remarkable effect.
- Summary
- Abstract
- Description
- Claims
- Application Information
AI Technical Summary
Problems solved by technology
Method used
Image
Examples
preparation example Construction
[0029] Core of the present invention is to provide a kind of method for preparing corrosion pit on metal material sample, and its preparation method comprises the following steps:
[0030] S1, sample processing blind hole: please refer to figure 1 , mark the position where the corrosion pit needs to be prepared in sample 1, use a bench drill to process the blind hole 2 at the marked position, the depth of the processed blind hole 2 is 0.3~0.4mm smaller than the target depth of the corrosion pit, and the processed blind hole 2 The diameter is 0.9~1.2mm smaller than the target diameter of the corrosion pit;
[0031] S2. Insulation and sealing treatment: Place the sample 1 with the blind hole processed in step S1 in analytical pure alcohol for 20 minutes for ultrasonic cleaning to remove the organic dirt on the surface, dry the sample after ultrasonic cleaning, and then immerse it in the burner. Heat the melted paraffin liquid until the surface of the sample is completely sealed...
Embodiment 1
[0038] (1) Test material: 35CrNiMoV low-alloy high-strength steel fatigue sample, the sample picture is as follows image 3 Shown: where the value of L1 is 118mm, the value of L2 is 30mm, the value of L3 is 28.02mm, the value of L4 is 10mm, the value of L5 is 20mm, A means that the arc radius here is 70mm, and the thickness of the sample is 4mm.
[0039] (2) Test objective: prepare a semi-elliptical corrosion pit about 5mm in length, 5mm in width and 1.5mm in depth in the center of the fatigue sample.
[0040] (3) Test method: S1. Prepare a 1.1mm deep blind hole with a Ф4mm diameter drill in the center of the fatigue sample;
[0041] S2. After cleaning the sample with alcohol, immerse it in heated and melted paraffin until the entire surface of the sample is completely sealed by paraffin, and remove the paraffin at the position of the blind hole with a metal pointed needle.
[0042] S3. Use the lead plate as the cathode, connect it to the negative pole of the DC constant cur...
Embodiment 2
[0045] (1) Test material: 7075 aluminum alloy four-point bending stress corrosion specimen, the sample diagram is as follows Figure 4 Shown: where the value of L6 is 70mm, the value of L7 is 10mm, and the thickness of the sample is 4mm.
[0046] (2) Test objective: prepare a semi-elliptical corrosion pit about 4mm in length, 4mm in width and 1.5mm in depth in the center of the fatigue sample.
[0047] (3) Test method: S1. Prepare a 1.1mm deep blind hole with a Ф3mm diameter drill in the center of the fatigue sample;
[0048] S2. After cleaning the sample with alcohol, immerse it in heated and melted paraffin until the entire surface of the sample is completely sealed by paraffin, and remove the paraffin at the position of the blind hole with a metal pointed needle.
PUM
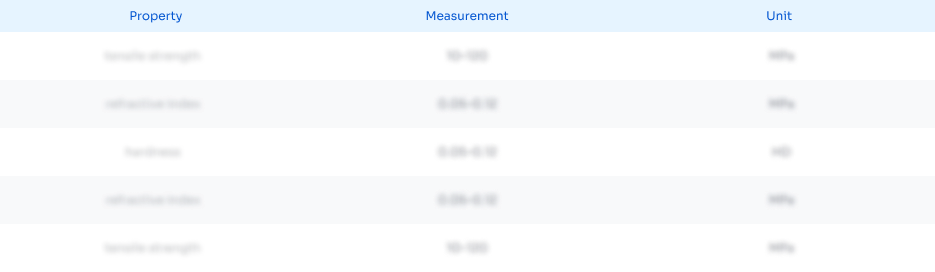
Abstract
Description
Claims
Application Information

- R&D
- Intellectual Property
- Life Sciences
- Materials
- Tech Scout
- Unparalleled Data Quality
- Higher Quality Content
- 60% Fewer Hallucinations
Browse by: Latest US Patents, China's latest patents, Technical Efficacy Thesaurus, Application Domain, Technology Topic, Popular Technical Reports.
© 2025 PatSnap. All rights reserved.Legal|Privacy policy|Modern Slavery Act Transparency Statement|Sitemap|About US| Contact US: help@patsnap.com