Vanadium-containing pig iron and method for preparing vanadium-containing pig iron by smelting vanadium-containing steel slag
A steel slag and pig iron technology, which is applied in the field of vanadium-containing pig iron and smelting vanadium-containing steel slag to produce vanadium-containing pig iron, can solve the problems of large-scale application limitations, high cost of vanadium extraction, low recovery rate, etc., and achieve reuse and adaptability of raw materials Strong, high recovery effect
- Summary
- Abstract
- Description
- Claims
- Application Information
AI Technical Summary
Problems solved by technology
Method used
Examples
Embodiment 1
[0052] After ball milling 64 parts of vanadium-containing steel slag, 32.01 parts of vanadium powder ore and other vanadium-containing materials, 1.60 parts of coke powder, 2.40 parts of dust removal ash, and appropriate amount of bentonite are added. After mixing and pelletizing, they are sent to sintering to obtain qualified Sinter. Then weigh 70 parts of sintered ore, 30 parts of vanadium-titanium magnetite lump ore, 25.26 parts of coke, and 6.96 parts of silica, and transfer them to a closed submerged arc furnace top transition bunker by a belt conveyor, and then drop to the rotating distributor to add to the furnace top bunker , Continuously add into the furnace through the material tube. The smelting temperature is controlled at 1650~1700℃, and the furnace mouth is opened every 2.5 hours to mix slag and iron. The obtained pig iron composition includes Fe 82.75%, C 7.48%, Si 4.98%, and V1.17%. The submerged arc furnace gas is recovered and used as the ignition heat sourc...
Embodiment 2
[0054] After ball milling 58.40 parts of vanadium-containing steel slag, 36.49 parts of vanadium powder ore and other vanadium-containing materials, mix with 2.19 parts of coke powder, 2.92 parts of dust removal ash, and add appropriate amount of bentonite. After mixing and pelletizing, it is sent to sintering to obtain qualified Sinter. Then weighed 75 parts of sintered ore, 25 parts of vanadium-titanium magnetite lump ore, 25.20 parts of coke, and 7.27 parts of silica, transferred by the belt conveyor to the transition silo on the top of the closed submerged arc furnace, and then dropped to the rotating distributor and added to the silo on the top of the furnace , Continuously add into the furnace through the material tube. The smelting temperature is controlled at 1650~1700℃, and the furnace mouth is opened every 2.5 hours to mix slag and iron. The obtained pig iron composition includes Fe 82.76%, C 7.49%, Si 4.99%, and V 1.16%. The submerged arc furnace gas is recovered a...
Embodiment 3
[0056] After ball milling 64.34 parts of vanadium-containing steel slag, 31 parts of vanadium powder ore and other vanadium-containing materials, mix with 1.56 parts of coke powder, 3.10 parts of dust removal ash, and add appropriate amount of cellulose. After mixing and pelletizing, it is sent to sintering, and it is qualified. Of sinter. Subsequently, 87.68 parts of sintered ore, 12.32 parts of vanadium-titanium magnetite lump ore, 22.24 parts of coke, and 7.95 parts of silica were weighed and transferred by the belt conveyor to the top transition bin of the closed submerged arc furnace, and then dropped to the rotating distributor and added to the top bin of the furnace , Continuously add into the furnace through the material tube. The smelting temperature is controlled at 1650~1700℃, and the furnace mouth is opened every 3 hours to mix slag and iron. The obtained pig iron composition includes Fe 81.96%, C 7.46%, Si 4.98%, and V 1.47%. The submerged arc furnace gas is reco...
PUM
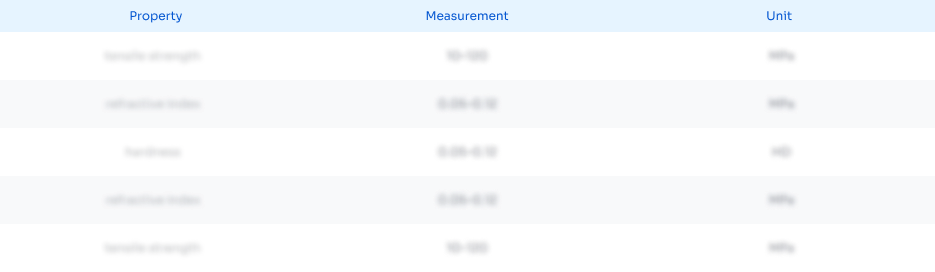
Abstract
Description
Claims
Application Information

- Generate Ideas
- Intellectual Property
- Life Sciences
- Materials
- Tech Scout
- Unparalleled Data Quality
- Higher Quality Content
- 60% Fewer Hallucinations
Browse by: Latest US Patents, China's latest patents, Technical Efficacy Thesaurus, Application Domain, Technology Topic, Popular Technical Reports.
© 2025 PatSnap. All rights reserved.Legal|Privacy policy|Modern Slavery Act Transparency Statement|Sitemap|About US| Contact US: help@patsnap.com