Core making method for barrel casting
A technology of castings and cylinders, which is applied in the field of casting, and can solve problems such as hindering the filling of molten metal, deteriorating the production environment, and strong odor of sawdust or foam boards.
- Summary
- Abstract
- Description
- Claims
- Application Information
AI Technical Summary
Problems solved by technology
Method used
Image
Examples
specific Embodiment
[0018] Specific examples: such as figure 1 As shown, a core-making method for cylindrical castings includes a core box 2, a chill iron and a hollow core bone 1 with holes, the chill iron is a direct external chill iron, and is a conformal chill iron 5 on the inner wall of a tubular casting, and the core The shape of the conformal cold iron 5 and the air outlet 7 is arranged on the box 2, and the appearance is assembled on the core box 2 in the form of loose pieces. The appearance of the conformal cold iron 5 and the air outlet 7 is integrated, and the height of the conformal cold iron pattern Greater than the thickness of the conformal chill 5 , the top of the air outlet pattern is in contact with the hole on the hollow core bone 1 . In order to conveniently pull out the integral conformal chill and air outlet pattern 3, according to the size of the conformal chill 5 and the sand core 4, the draft angle of the conformal chill can be 15°~45°, The draft angle of the air outlet ...
PUM
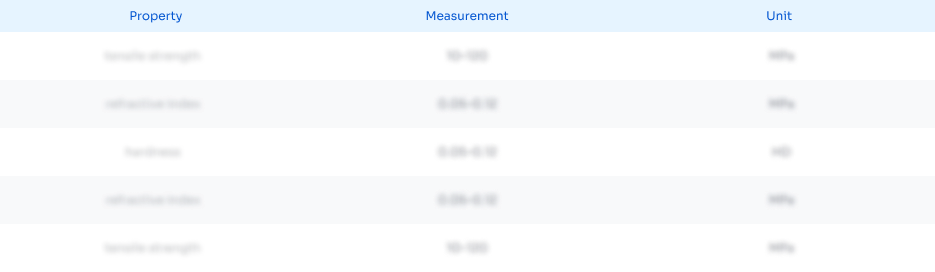
Abstract
Description
Claims
Application Information

- Generate Ideas
- Intellectual Property
- Life Sciences
- Materials
- Tech Scout
- Unparalleled Data Quality
- Higher Quality Content
- 60% Fewer Hallucinations
Browse by: Latest US Patents, China's latest patents, Technical Efficacy Thesaurus, Application Domain, Technology Topic, Popular Technical Reports.
© 2025 PatSnap. All rights reserved.Legal|Privacy policy|Modern Slavery Act Transparency Statement|Sitemap|About US| Contact US: help@patsnap.com