Integral molding method for vertical-rib composite material stiffened wallboard through autoclave
A technology of composite materials and reinforced wall panels, which is applied to other household appliances, household appliances, household components, etc., can solve the problems of difficult manufacturing, long manufacturing cycle, large deviation, etc., and achieve short manufacturing cycle, good internal quality, light weight effect
- Summary
- Abstract
- Description
- Claims
- Application Information
AI Technical Summary
Problems solved by technology
Method used
Image
Examples
specific Embodiment approach 1
[0029] Specific implementation mode one: as Figure 1-Figure 9 As shown, this embodiment discloses a method for integrally forming an autoclave of a composite material reinforced wall panel with vertical ribs, and the method includes the following steps:
[0030] Step 1: Manufacturing a soft mold 9;
[0031] 1.1, according to the inner surface of the product (i.e. the composite material reinforced wallboard with vertical ribs), the soft mold forming tooling is manufactured; when the soft mold forming tooling is designed, the positioning of the soft mold 9 and the product when it is solidified (positioning hole or positioning Groove), and design the product edge line and margin line according to the product technical requirements;
[0032] 1.2. Off-line prepreg according to the allowance of soft molding tooling;
[0033] 1.3. Lay the prepreg laid in advance on the soft mold forming tooling. When the prepreg is laid, each layer is vacuumed (the number of layers of the prepreg ...
PUM
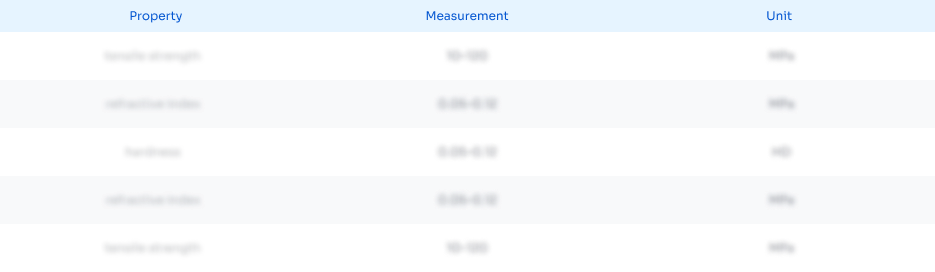
Abstract
Description
Claims
Application Information

- Generate Ideas
- Intellectual Property
- Life Sciences
- Materials
- Tech Scout
- Unparalleled Data Quality
- Higher Quality Content
- 60% Fewer Hallucinations
Browse by: Latest US Patents, China's latest patents, Technical Efficacy Thesaurus, Application Domain, Technology Topic, Popular Technical Reports.
© 2025 PatSnap. All rights reserved.Legal|Privacy policy|Modern Slavery Act Transparency Statement|Sitemap|About US| Contact US: help@patsnap.com