Exhaust system of silicon carbide smelting workshop
An exhaust system and silicon carbide technology, which is applied in the field of exhaust systems, can solve problems such as increasing the cost of silicon carbide smelting, environmental hazards in smelting workshops, and the inability to flexibly handle exhaust, so as to achieve improved exhaust effects, long service life, and energy saving Energy and Cost Effects
- Summary
- Abstract
- Description
- Claims
- Application Information
AI Technical Summary
Problems solved by technology
Method used
Image
Examples
Embodiment Construction
[0017] Such as Figure 1 to Figure 4 As shown, an exhaust system of a silicon carbide smelting workshop includes a smelting workshop 1, a smelting furnace 6 arranged in the smelting workshop 1; a gas collection building 2, a first exhaust mechanism 3-1, a second exhaust Mechanism 3-2, third connecting pipe 3-31, third valve 3-32, dust removal tower 4 and elbow pipe 5; the first exhaust mechanism 3-1 includes the first main air blower arranged outside the side wall of the smelting workshop 1 Pipe 3-11, first connecting pipe 3-12, first valve 3-13, first induced draft fan 3-14, and first branch air pipe 3-15 arranged outside the top wall of smelting workshop 1; the second row The gas mechanism 3-2 includes the second main air duct 3-21, the second connecting pipe 3-22, the second valve 3-23, the second induced draft fan 3-24 arranged outside the side wall of the smelting workshop 1, and the The second branch air duct 3-25 outside the top wall of the smelting workshop 1.
[001...
PUM
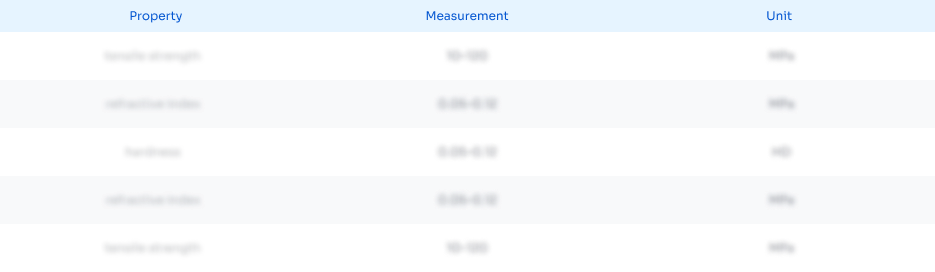
Abstract
Description
Claims
Application Information

- R&D
- Intellectual Property
- Life Sciences
- Materials
- Tech Scout
- Unparalleled Data Quality
- Higher Quality Content
- 60% Fewer Hallucinations
Browse by: Latest US Patents, China's latest patents, Technical Efficacy Thesaurus, Application Domain, Technology Topic, Popular Technical Reports.
© 2025 PatSnap. All rights reserved.Legal|Privacy policy|Modern Slavery Act Transparency Statement|Sitemap|About US| Contact US: help@patsnap.com