Method for preparing high-gelling-activity steel slag through high-temperature reconstruction of calcium-aluminum components and application thereof
A technology of steel slag and calcium aluminum, applied in the field of green building materials, can solve the problems that the chemical composition and mineral composition of steel slag have not been fundamentally changed, and the resource utilization rate of steel slag is less than 30%.
- Summary
- Abstract
- Description
- Claims
- Application Information
AI Technical Summary
Problems solved by technology
Method used
Image
Examples
Embodiment 1
[0030] (1) The raw material is composed of steel slag, lime and bauxite, and the mass percentage content of each component is as follows: steel slag 83%, calcium oxide 11%, bauxite 6%
[0031] (2) Dry the steel slag and calcium-aluminum quenched and tempered components at 110°C for 8 hours, crush them with a crusher to a particle size of <10mm, and grind them with a ball mill to a specific surface area of 400±20㎡ / Kg
[0032] (3) Put the steel slag prepared in step (2) into the mixer according to the ratio of step (1) for mixing, so that each component is evenly mixed, and the uniformly mixed material is made into a round cake test piece and placed in a resistor Calcination in furnace, calcination temperature 1350℃, holding time 90min, after the heat preservation is over, air cooling, and then grind the test block to a specific surface area of 400±20㎡ / Kg, to obtain the reconstituted steel slag of the calcium-aluminum component clinker.
Embodiment 2
[0034] (1) The raw material is composed of steel slag, lime and bauxite, and the mass percentage content of each component is as follows: steel slag 77%, calcium oxide 19%, bauxite 4%
[0035] (2) Dry the steel slag and calcium-aluminum quenched and tempered components at 110°C for 8 hours, crush them with a crusher to a particle size of <10mm, and grind them with a ball mill to a specific surface area of 400±20㎡ / Kg.
[0036] (3) Put the steel slag prepared in step (2) into the mixer according to the ratio of step (1) for mixing, so that each component is evenly mixed, and the uniformly mixed material is made into a round cake test piece and placed in a resistor Calcination in furnace, calcination temperature 1350℃, holding time 90min, after the heat preservation is over, air cooling, and then grind the test block to a specific surface area of 400±20㎡ / Kg, to obtain the reconstituted steel slag of the calcium-aluminum component clinker.
Embodiment 3
[0038] (1) The raw material is composed of steel slag, lime and bauxite, and the mass percentage content of each component is as follows: steel slag 74%, calcium oxide 24%, bauxite 2%
[0039] (2) Dry the steel slag and calcium-aluminum quenched and tempered components at 110°C for 8 hours, crush them with a crusher to a particle size of <10mm, and grind them with a ball mill to a specific surface area of 400±20㎡ / Kg.
[0040](3) Put the steel slag prepared in step (2) into the mixer according to the ratio of step (1) for mixing, so that each component is evenly mixed, and the uniformly mixed material is made into a round cake test piece and placed in a resistor Calcination in furnace, calcination temperature 1350℃, holding time 90min, after the heat preservation is over, air cooling, and then grind the test block to a specific surface area of 400±20㎡ / Kg, to obtain the reconstituted steel slag of the calcium-aluminum component clinker.
[0041] The ground steel slag was su...
PUM
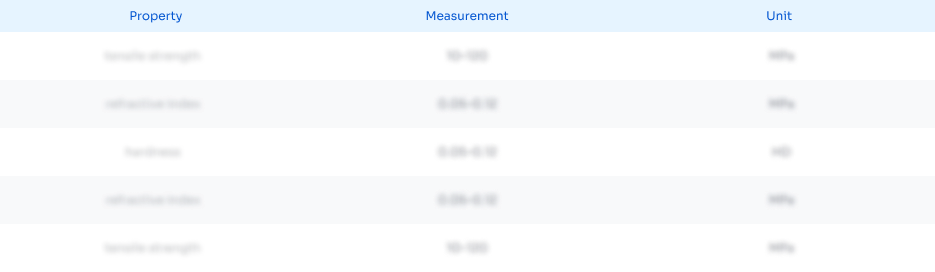
Abstract
Description
Claims
Application Information

- R&D
- Intellectual Property
- Life Sciences
- Materials
- Tech Scout
- Unparalleled Data Quality
- Higher Quality Content
- 60% Fewer Hallucinations
Browse by: Latest US Patents, China's latest patents, Technical Efficacy Thesaurus, Application Domain, Technology Topic, Popular Technical Reports.
© 2025 PatSnap. All rights reserved.Legal|Privacy policy|Modern Slavery Act Transparency Statement|Sitemap|About US| Contact US: help@patsnap.com