Preparation method of modified sodium alginate/polyacrylic acid composite thickener
A composite thickener, sodium alginate technology, applied in dyeing, textiles and papermaking, etc., can solve the problems of poor rheology of sodium alginate, poor rheology of sodium alginate original paste, low Newtonian viscosity and low structural viscosity, etc. , to achieve the effect of improving thickening performance and electrolyte resistance
- Summary
- Abstract
- Description
- Claims
- Application Information
AI Technical Summary
Problems solved by technology
Method used
Image
Examples
Embodiment 1
[0023] (1) Add sodium alginate to a three-neck flask equipped with a stirrer, reflux device, and dropping funnel, and then add an appropriate amount of deionized water. The mass ratio of deionized water to sodium alginate is 30:1, so that the alginic acid The sodium is completely dissolved; adjust the pH to 8 with a 50% mass fraction of sodium hydroxide solution, slowly add allyl glycidyl ether, the mass ratio of allyl alcohol glycidyl ether to sodium alginate is 0.8:1, and heat in a water bath to 70°C, react for 10h, after the reaction is over, cool to room temperature, adjust the pH of the solution to 4 with glacial acetic acid with a mass fraction of 50%, add acetone and let it stand for 12h, remove the water and unreacted allyl glycidyl ether in the mixture, After the product is precipitated, filter, then stand still with acetone for 12 hours, filter, collect the solid, vacuum dry at 50°C for 24 hours, and set aside;
[0024] (2) Add acrylic acid, modified sodium alginate ...
Embodiment 2
[0034] (1) Add sodium alginate to a three-neck flask equipped with a stirrer, reflux device, and dropping funnel, and then add an appropriate amount of deionized water. The mass ratio of deionized water to sodium alginate is 50:1, so that alginic acid The sodium is completely dissolved; adjust the pH to 10 with a 50% mass fraction of sodium hydroxide solution, slowly add allyl glycidyl ether, the mass ratio of allyl alcohol glycidyl ether to sodium alginate is 1.2:1, and heat in a water bath to 80°C, react for 7 hours, after the reaction, cool to room temperature, adjust the pH of the solution to 5 with glacial acetic acid with a mass fraction of 50%, add acetone and let stand for 12 hours, remove the water and unreacted allyl glycidyl ether in the mixture, After the product is precipitated, filter, then stand still with acetone for 12 hours, filter, collect the solid, vacuum dry at 70°C for 12 hours, and set aside;
[0035] (2) Add methacrylic acid, modified sodium alginate a...
Embodiment 3
[0038] (1) Add sodium alginate to a three-necked flask equipped with a stirrer, reflux device, and dropping funnel, and then add an appropriate amount of deionized water. The mass ratio of deionized water to sodium alginate is 40:1, so that alginic acid The sodium is completely dissolved; adjust the pH to 9 with a 50% mass fraction of sodium hydroxide solution, slowly add allyl glycidyl ether, the mass ratio of allyl alcohol glycidyl ether to sodium alginate is 1:1, and heat in a water bath to React at 75°C for 8 hours. After the reaction, cool to room temperature, adjust the pH of the solution to 4.5 with glacial acetic acid with a mass fraction of 50%, add acetone and let stand for 12 hours, remove the water and unreacted allyl glycidyl ether in the mixture, After the product is precipitated, filter, then stand still with acetone for 12 hours, filter, collect the solid, vacuum dry at 60°C for 18 hours, and set aside;
[0039] (2) Add acrylic acid, modified sodium alginate an...
PUM
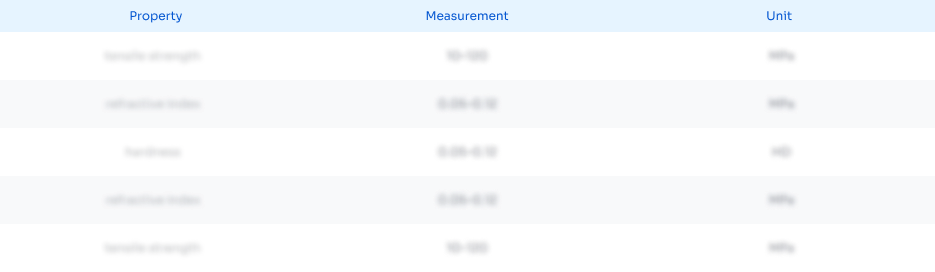
Abstract
Description
Claims
Application Information

- R&D Engineer
- R&D Manager
- IP Professional
- Industry Leading Data Capabilities
- Powerful AI technology
- Patent DNA Extraction
Browse by: Latest US Patents, China's latest patents, Technical Efficacy Thesaurus, Application Domain, Technology Topic, Popular Technical Reports.
© 2024 PatSnap. All rights reserved.Legal|Privacy policy|Modern Slavery Act Transparency Statement|Sitemap|About US| Contact US: help@patsnap.com