Synergistic recycling method of zinc-rich metallurgical dust sludge and semidry desulfurization ash
A semi-dry desulfurization, metallurgical dust sludge technology, applied in chemical instruments and methods, alkali metal chlorides, zinc oxide/zinc hydroxide, etc., to achieve the effect of high free alkali content and complex components
- Summary
- Abstract
- Description
- Claims
- Application Information
AI Technical Summary
Problems solved by technology
Method used
Image
Examples
example 1
[0019] The main components of semi-dry desulfurization ash and blast furnace gas ash from a steel plant in Shandong (the range listed in the example is the range of multiple tests, the same below) are: blast furnace gas ash TFe 26.53% ~ 26.65%, SiO 2 5.51%~5.89%, ZnO 4.45%~4.84%, Al 2 o 3 2.91%~3.22%, CaO 3.07%~3.93%, MgO 0.06%~0.16%; semi-dry desulfurization ash TFe 5.56%~5.61%, SiO 2 10.59%~11.20%, Al 2 o 3 0.81%-1.19%, CaO 32.21%-39.96%, MgO 0.35%-1.09%.
[0020] Use process:
[0021] (1) Mix the ingredients. Take 1kg of blast furnace gas ash, mix it with semi-dry desulfurization ash according to the mass ratio of 1:0.35~0.5, make pellets, and after drying, oxidize and sinter at 1250℃~1260℃ to collect smoke and dust to produce sinter.
[0022] (2) Recovery of zinc oxide. The soot is treated by gravity separation, and the ZnO grade of the product is 96.25% to 96.63%.
[0023] (3) extract potassium chloride. Gravity separation water is recycled to enrich soluble ...
example 2
[0028] Semi-dry desulfurization ash and blast furnace gas ash from a steel plant in Inner Mongolia. The main components are: blast furnace gas ash TFe 26.11%-28.35%, ZnO 4.22%-4.67%, SiO 2 4.53%~5.12%, Al 2 o 3 2.22%~2.26%, CaO3.66%~3.75%, MgO 0.38%~0.65%; semi-dry desulfurization ash TFe 3.55%~4.21%, SiO 2 11.22%~11.37%, Al 2 o 3 0.71%-1.37%, CaO 35.42%-38.59%, MgO 0.22%-1.17%.
[0029] Use process:
[0030] (1) Mix the ingredients. Take 1kg of blast furnace gas ash, mix it with semi-dry desulfurization ash according to the mass ratio of 1:0.36~0.55, make pellets, and after drying, oxidize and sinter at 1280℃~1300℃ to produce sintered ore.
[0031] (2) Recovery of zinc oxide. The soot is treated by gravity separation, and the ZnO grade of the product is 94.53% to 96.16%.
[0032] (3) Selective crushing. After the sinter is cooled, use roller crushing equipment to crush the sinter to 0.55mm-0.6mm, and selectively dissociate calcium ferrite and gypsum.
[0033] (4...
example 3
[0037] Semi-dry desulfurization ash and blast furnace gas ash from a steel plant in Guangxi, the main components are: blast furnace gas ash TFe 28.53%-26.65%, SiO 2 5.51%~5.89%, ZnO 6.81%~8.26%, Al 2 o 3 2.91%~3.22%, CaO 3.07%~3.93%, MgO 0.06%~0.16%; semi-dry desulfurization ash TFe 5.53%~6.07%, SiO 2 10.73%~10.81%, Al 2 o 3 0.97%-1.49%, CaO 36.42%-39.01%, MgO 0.39%-0.79%.
[0038] Use process:
[0039] (1) Mix the ingredients. 5kg of blast furnace gas ash is mixed with semi-dry desulfurization ash at a mass ratio of 1:0.56-0.68 to make pellets. After drying, it is oxidized and sintered at 1230°C-1260°C to collect smoke and dust to produce sintered ore.
[0040] (2) Recovery of zinc oxide. The soot is treated by gravity separation, and the ZnO grade of the product is 98.12% to 98.46%.
[0041] (2) Selective crushing. After the sinter is cooled, use roller crushing equipment to crush the sinter to 3.5mm-3.8mm, and selectively dissociate calcium ferrite and gypsum. ...
PUM
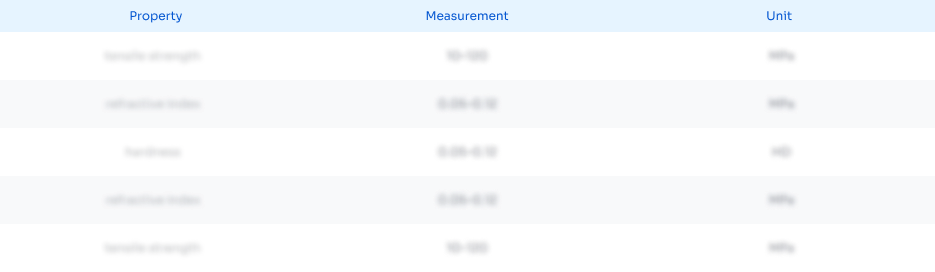
Abstract
Description
Claims
Application Information

- R&D Engineer
- R&D Manager
- IP Professional
- Industry Leading Data Capabilities
- Powerful AI technology
- Patent DNA Extraction
Browse by: Latest US Patents, China's latest patents, Technical Efficacy Thesaurus, Application Domain, Technology Topic, Popular Technical Reports.
© 2024 PatSnap. All rights reserved.Legal|Privacy policy|Modern Slavery Act Transparency Statement|Sitemap|About US| Contact US: help@patsnap.com