Self-made grinding aid
A technology of grinding aid and triethanolamine, which is applied in the field of cement production grinding aids, can solve the problems that the expected use effect cannot be achieved and the cost of grinding aids is high, and can improve the grinding process, improve the flow rate of materials, and eliminate static electricity in the mill. Effect
- Summary
- Abstract
- Description
- Claims
- Application Information
AI Technical Summary
Problems solved by technology
Method used
Image
Examples
Embodiment 1
[0019] A self-made grinding aid, its raw material components are as follows: ethylene glycol: 8kg, triethanolamine: 15kg, glycerin residue: 15kg, sodium acetate: 1kg, industrial salt: 1kg, lignin: 2kg, water: 58kg.
[0020] Its preparation method is as follows:
[0021] Step 1: Control the temperature of water at 40°C during preparation, add glycerin residue and triethanolamine and mix evenly;
[0022] Step 2: In step 1, add glycerin residue and triethanolamine to the water and mix evenly, then add ethylene glycol, sodium acetate, lignin, and industrial salt in sequence.
Embodiment 2
[0024] A self-made grinding aid, its raw material components are as follows: ethylene glycol: 10kg, triethanolamine: 20kg, glycerin residue: 20kg, sodium acetate: 1.5kg, industrial salt: 1kg, lignin: 2.5kg, water: 45kg.
[0025] Its preparation method is as follows:
[0026] Step 1: Control the temperature of water at 42°C during preparation, add glycerin residue and triethanolamine and mix evenly;
[0027] Step 2: In step 1, add glycerin residue and triethanolamine to the water and mix evenly, then add ethylene glycol, sodium acetate, lignin, and industrial salt in sequence.
Embodiment 3
[0029] A self-made grinding aid, its raw material components are as follows: ethylene glycol: 12kg, triethanolamine: 25kg, glycerin residue: 25kg, sodium acetate: 1.5kg, industrial salt: 1.5kg, lignin: 3kg, water: 32kg.
[0030] Its preparation method is as follows:
[0031] Step 1: Control the temperature of water at 43°C during preparation, add glycerin residue and triethanolamine and mix evenly;
[0032] Step 2: In step 1, add glycerin residue and triethanolamine to the water and mix evenly, then add ethylene glycol, sodium acetate, lignin, and industrial salt in sequence.
PUM
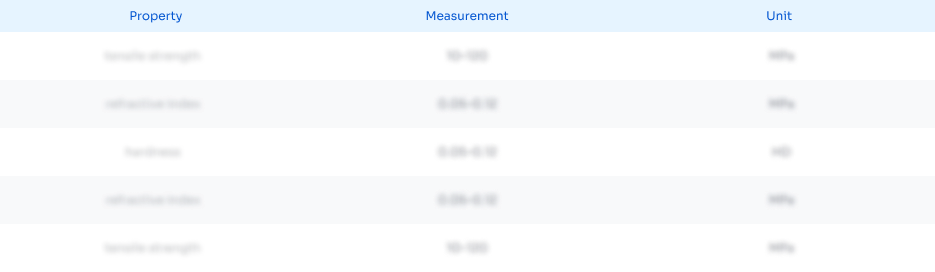
Abstract
Description
Claims
Application Information

- R&D
- Intellectual Property
- Life Sciences
- Materials
- Tech Scout
- Unparalleled Data Quality
- Higher Quality Content
- 60% Fewer Hallucinations
Browse by: Latest US Patents, China's latest patents, Technical Efficacy Thesaurus, Application Domain, Technology Topic, Popular Technical Reports.
© 2025 PatSnap. All rights reserved.Legal|Privacy policy|Modern Slavery Act Transparency Statement|Sitemap|About US| Contact US: help@patsnap.com