Preparation method of nano-cellulose grafted epoxy group
A technology of nanocellulose and epoxy groups, which is applied in the field of preparation of nanocellulose grafted epoxy groups, can solve the problems of large specific surface area, easy intertwining of fibers, self-agglomeration, etc., and achieve reduced agglomeration, easy operation, Effect of Dispersion Improvement
- Summary
- Abstract
- Description
- Claims
- Application Information
AI Technical Summary
Problems solved by technology
Method used
Examples
Embodiment 1
[0014] A method for preparing nano-cellulose grafted epoxy groups, comprising the following steps: preparing 80 parts of sulfuric acid solution with a mass fraction of 64%, adding 15 parts of microcrystalline cellulose, ultrasonically stirring at 42°C for 55 minutes, adding 190 parts of Terminate the reaction with ionized water, and repeatedly centrifuge and wash until the pH value is neutral, and dialyze until the conductivity is constant to obtain NCC slurry, freeze-dry and disperse at -75°C to obtain NCC; disperse 10 parts of NCC in 65 parts of DMAc, Under nitrogen atmosphere, after heating to 45°C, add 16 parts of CDI, stir and react for 10 hours, then add 15 parts of ECH to the reaction system, continue to react for 12 hours, then use absolute ethanol to repeatedly centrifuge and wash, freeze-dry the product, and disperse Obtained; All raw materials are parts by weight.
Embodiment 2
[0016] A method for preparing nano-cellulose grafted epoxy groups, comprising the following steps: preparing 75 parts of sulfuric acid solution with a mass fraction of 64%, adding 10 parts of microcrystalline cellulose, and reacting with ultrasonic stirring at 40°C for 50 minutes, adding 180 parts of Terminate the reaction with ionized water, and repeatedly centrifuge and wash until the pH value is neutral, and dialyze until the conductivity is constant to obtain NCC slurry, freeze-dry and disperse at -75°C to obtain NCC; disperse 5 parts of NCC in 60 parts of DMAc, Under nitrogen atmosphere, after heating to 44°C, add 14 parts of CDI, stir and react for 9 hours, then add 10 parts of ECH to the reaction system, continue to react for 11 hours, then use absolute ethanol to repeatedly centrifuge and wash, freeze-dry the product, and disperse Obtained; All raw materials are parts by weight.
Embodiment 3
[0018] A method for preparing nano-cellulose grafted epoxy groups, comprising the steps of: preparing 85 parts of sulfuric acid solution with a mass fraction of 64%, adding 20 parts of microcrystalline cellulose, ultrasonically stirring at 44°C for 60 minutes, adding 200 parts of Terminate the reaction with ionized water, and repeatedly centrifuge and wash until the pH value is neutral, and dialyze until the conductivity is constant to obtain NCC slurry, freeze-dry and disperse at -75°C to obtain NCC; disperse 15 parts of NCC in 70 parts of DMAc, Under nitrogen atmosphere, after heating to 46°C, add 18 parts of CDI, stir and react for 11 hours, then add 20 parts of ECH to the reaction system, continue to react for 13 hours, then repeatedly centrifuge and wash with absolute ethanol, freeze-dry the product, and disperse Obtained; All raw materials are parts by weight.
[0019] The method is simple, fast, and easy to operate. Nanocellulose grafted with epoxy groups is successfull...
PUM
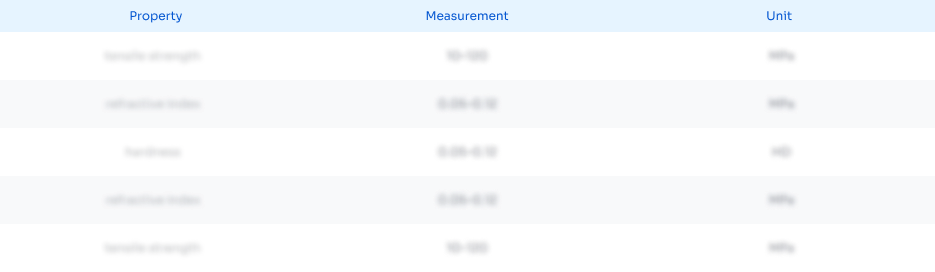
Abstract
Description
Claims
Application Information

- Generate Ideas
- Intellectual Property
- Life Sciences
- Materials
- Tech Scout
- Unparalleled Data Quality
- Higher Quality Content
- 60% Fewer Hallucinations
Browse by: Latest US Patents, China's latest patents, Technical Efficacy Thesaurus, Application Domain, Technology Topic, Popular Technical Reports.
© 2025 PatSnap. All rights reserved.Legal|Privacy policy|Modern Slavery Act Transparency Statement|Sitemap|About US| Contact US: help@patsnap.com