Five-axis digital-controlled inner container pipe winding machine
A technology for winding tubes and inner tubes is applied in the field of five-axis numerical control tube winding machines for inner tubes, which can solve the problems of affecting the effect of tube winding, the difficulty of winding the object to be wound around the tube, and the uneven winding of the tube. Good effect, precise control effect
- Summary
- Abstract
- Description
- Claims
- Application Information
AI Technical Summary
Problems solved by technology
Method used
Image
Examples
Embodiment
[0024] see Figure 1-3 , the present invention provides a technical solution: a five-axis numerical control liner tube winding machine, including a longitudinal servo slide rail 1, a transverse servo slide rail 2 and a radial servo slide rail 3, the longitudinal servo slide rail 1 is set vertically, and the horizontal servo slide rail The servo slide rail 2 is horizontally connected to the moving end of the longitudinal servo slide rail 1, the radial servo slide rail 3 is installed radially on the moving end of the horizontal servo slide rail 2, and the bottom of the moving end of the radial servo slide rail 3 is connected with a second A mounting seat 4, the bottom of the first mounting seat 4 is equipped with a longitudinal rotating shaft 5, the bottom of the longitudinal rotating shaft 5 is connected with a second mounting seat 8, the bottom end of the second mounting seat 8 is equipped with a rotating shaft seat 9, and the inner horizontal direction of the rotating shaft se...
PUM
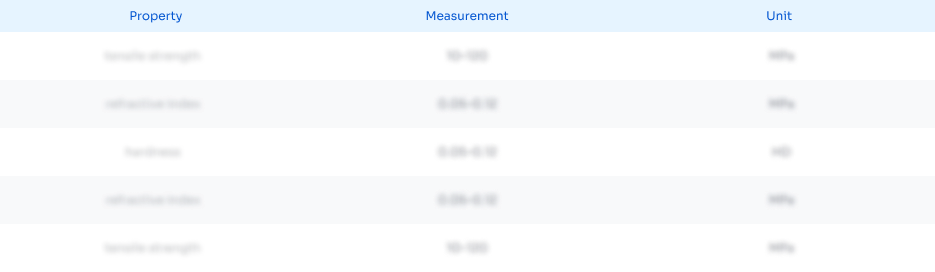
Abstract
Description
Claims
Application Information

- R&D Engineer
- R&D Manager
- IP Professional
- Industry Leading Data Capabilities
- Powerful AI technology
- Patent DNA Extraction
Browse by: Latest US Patents, China's latest patents, Technical Efficacy Thesaurus, Application Domain, Technology Topic, Popular Technical Reports.
© 2024 PatSnap. All rights reserved.Legal|Privacy policy|Modern Slavery Act Transparency Statement|Sitemap|About US| Contact US: help@patsnap.com