Preparation method for biomass-based carbon nanofiber
A technology of carbon nanofibers and biomass, applied in the direction of nanotechnology, nanotechnology, fiber chemical characteristics, etc., can solve the problems of poor electrochemical performance and achieve the effect of enhancing electrochemical properties
- Summary
- Abstract
- Description
- Claims
- Application Information
AI Technical Summary
Problems solved by technology
Method used
Image
Examples
preparation example Construction
[0026] The method for preparing biomass-based carbon nanofibers of the present invention is specifically implemented according to the following steps:
[0027] Step 1. Mix lignin, butyric anhydride and 1-methylimidazole uniformly, and stir the reaction under nitrogen atmosphere. The reaction temperature is 40~80℃, and the reaction time is 4~12h. After the reaction is over, naturally cool to room temperature. Obtain a mixed solution; then the mixed solution is precipitated with n-hexane and washed 4-6 times, filtered to obtain a filter residue, and finally the filter residue is placed in deionized water, and stirred for 24h on a magnetic stirrer, filtered with suction, and freeze-dried to obtain esterification Modified lignin;
[0028] The mass ratio of lignin to butyric anhydride is 1-10: 1-5; the mass of 1-methylimidazole is 1 to 5% of the mass of lignin;
[0029] The mass ratio of filter residue to deionized water is 1:1000;
Embodiment 1
[0042] Firstly, 20 g of lignin, 40 g of butyric anhydride and 0.5 g of 1-methylimidazole were weighed into a 250 ml three-necked flask, stirred under a nitrogen atmosphere, the reaction temperature was 60° C., and the reaction time was 8 hours. After the reaction, the mixture was naturally cooled to room temperature, and the mixture was transferred to a large beaker of 1 L, and washed with 500 mL of n-hexane for 4 to 6 times, and each washing was fully stirred with a glass rod. Finally, the washed lignin suspension was placed in 500 mL of deionized water, and stirred on a magnetic stirrer for 24 hours. Then the mixture of water and lignin is filtered and dried to obtain esterified modified lignin. Spinning solution configuration: the total polymer mass fraction of the spinning solution is 20%, and the mass ratio of polyacrylonitrile to lignin is 40:60. First add the required amount of polyacrylonitrile to N,N-dimethylformamide, stir for a period of time at a speed of 600rpm at...
Embodiment 2
[0044] First, weigh 10g of lignin, 30g of butyric anhydride and 0.3g of 1-methylimidazole into a 250ml three-necked flask, stir under nitrogen atmosphere, reaction temperature 80°C, reaction time 4h. After the reaction, the mixture was naturally cooled to room temperature, and the mixed solution was transferred to a large beaker of 1 L, washed with 500 mL of n-hexane several times and fully stirred. Finally, the washed lignin was placed in 500 mL of deionized water and stirred for 12 hours using a magnetic stirrer. After suction filtration and freeze-drying, esterified modified lignin is obtained. Spinning solution configuration: the total polymer mass fraction of the spinning solution is 10%, and the ratio of polyacrylonitrile to lignin is 50:50. First add the required amount of polyacrylonitrile to N,N-dimethylformamide, stir for a period of time at 200 rpm at 40°C until the PAN is completely dissolved, and then add the corresponding amount of lignin to the polyacrylonitrile...
PUM
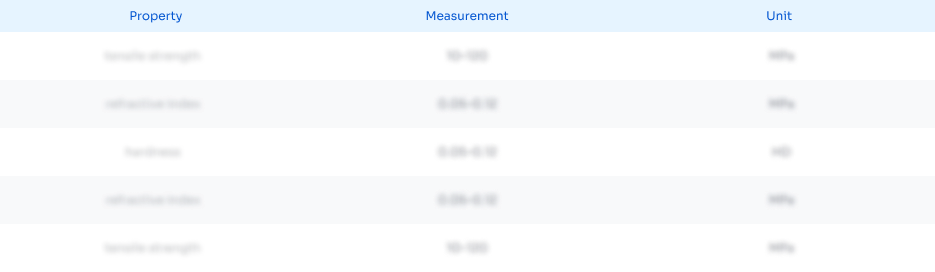
Abstract
Description
Claims
Application Information

- R&D
- Intellectual Property
- Life Sciences
- Materials
- Tech Scout
- Unparalleled Data Quality
- Higher Quality Content
- 60% Fewer Hallucinations
Browse by: Latest US Patents, China's latest patents, Technical Efficacy Thesaurus, Application Domain, Technology Topic, Popular Technical Reports.
© 2025 PatSnap. All rights reserved.Legal|Privacy policy|Modern Slavery Act Transparency Statement|Sitemap|About US| Contact US: help@patsnap.com