Method for rapidly laying auxiliary materials
A technology of auxiliary materials and laying, which is applied to other household appliances, household appliances, household components, etc., can solve the problems of long time-consuming fixing, long laying of auxiliary materials, and increased labor force, so as to reduce the labor force of employees and reduce auxiliary materials. The effect of laying the number of materials and improving work efficiency
- Summary
- Abstract
- Description
- Claims
- Application Information
AI Technical Summary
Problems solved by technology
Method used
Image
Examples
Embodiment Construction
[0025] The technical solutions of the present invention will be further specifically described below through embodiments and in conjunction with the accompanying drawings.
[0026] see Figure 1-Figure 4 As shown, a method for quickly laying auxiliary materials according to the present invention mainly includes the following steps:
[0027] 1. First, the PVC triangular runner and the runner backing plate are made into an integral molding structure 2 by using a molding process, (such as image 3 and Figure 4 shown) Among them, at the position where there is a glue injection port, the glue guide port can be fixedly placed above the triangular flow channel (such as Figure 4 As shown) form another integral molding structure 1; in this specific embodiment, the PVC triangular flow channel and the flow channel backing plate can be combined by bonding or snap-in structure.
[0028] In this step, under normal circumstances, in order to facilitate mass production and control costs,...
PUM
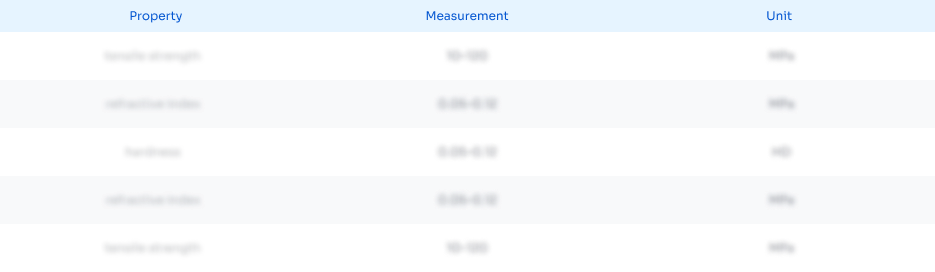
Abstract
Description
Claims
Application Information

- Generate Ideas
- Intellectual Property
- Life Sciences
- Materials
- Tech Scout
- Unparalleled Data Quality
- Higher Quality Content
- 60% Fewer Hallucinations
Browse by: Latest US Patents, China's latest patents, Technical Efficacy Thesaurus, Application Domain, Technology Topic, Popular Technical Reports.
© 2025 PatSnap. All rights reserved.Legal|Privacy policy|Modern Slavery Act Transparency Statement|Sitemap|About US| Contact US: help@patsnap.com