A kind of steel structure automatic welding production method
A technology of automatic welding and production methods, applied in the direction of welding equipment, welding equipment, auxiliary welding equipment, etc., can solve the problems of long construction period and low efficiency, and achieve the effect of good welding quality, simple process and improved efficiency
- Summary
- Abstract
- Description
- Claims
- Application Information
AI Technical Summary
Problems solved by technology
Method used
Image
Examples
Embodiment 1
[0050] This embodiment discloses a steel structure automatic welding production method, the method includes the following steps:
[0051] S1. Place the profiled steel on the buffer lifting conveying roller line 1 at the highest position;
[0052] S2. The buffer lifting conveying roller line 1 descends to drop the profiled steel onto the first transverse conveyor 4, and the first transverse conveyor 4 laterally sends the profiled steel to the top of the first lifting conveying roller line 22 at the lowest position;
[0053] S3, the first lifting conveying roller line 2 rises to support the section steel, and the section steel is sent to the automatic cutting machine 6 for fixed-length cutting by the fixed-length cutting feeding mechanism;
[0054] S4. The section steel cut to length is conveyed by the second lifting conveying roller line 8; and the remaining material and waste are sent to the remaining material buffer area 9 and the waste material buffer area 10 respectively by...
Embodiment 2
[0079] This embodiment discloses the automatic welding production line that realizes above-mentioned automatic welding production method, as Figure 1 to Figure 5 As shown, an automatic welding production line for steel structures includes a buffer lifting conveyor line 1 and a first lifting conveyor roller line 2 parallel to each other, and a first Horizontal conveyor 4; the downstream of the first lifting conveying roller line 2 is provided with an automatic cutting machine 6, and the side of the first lifting conveying roller line 2 is provided with a fixed-length cutting feeding mechanism 3;
[0080] Among them, the specific structures of the lifting and conveying roller lines mentioned in the embodiment of the present invention (the cache lifting and conveying roller line 1, the first to the seventh lifting and conveying roller lines 25) are all the same, and they all include several lifting and conveying roller group units , each elevating conveying roller group unit is ...
PUM
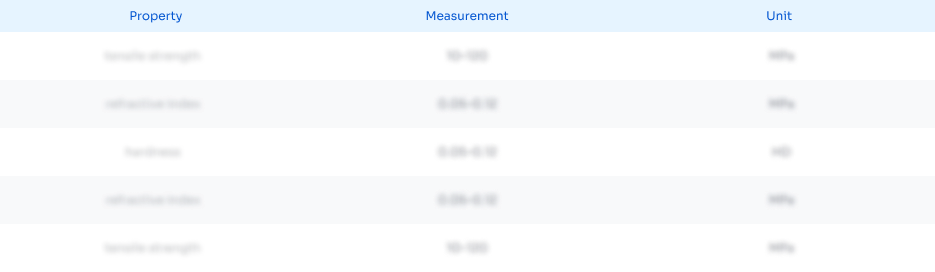
Abstract
Description
Claims
Application Information

- R&D
- Intellectual Property
- Life Sciences
- Materials
- Tech Scout
- Unparalleled Data Quality
- Higher Quality Content
- 60% Fewer Hallucinations
Browse by: Latest US Patents, China's latest patents, Technical Efficacy Thesaurus, Application Domain, Technology Topic, Popular Technical Reports.
© 2025 PatSnap. All rights reserved.Legal|Privacy policy|Modern Slavery Act Transparency Statement|Sitemap|About US| Contact US: help@patsnap.com