Film coating method for television backboard
A TV and film-coating technology, which is applied to color TV parts, TV system parts, TVs, etc., can solve problems such as lower production efficiency, cumbersome production processes, and complicated TV backplane structure, and achieve improved substrate Quality, improvement of film processing efficiency, and stable bonding force
- Summary
- Abstract
- Description
- Claims
- Application Information
AI Technical Summary
Problems solved by technology
Method used
Examples
Embodiment 1
[0022] This embodiment proposes a method for laminating a television backplane, comprising the following steps:
[0023] Step 1: Select the steel with steel quality requirements of DX53D+Z and above, and the surface requirements of FB grade and above quality standards as the substrate;
[0024] Step 2: Pretreat the substrate, including degreasing, brushing and rinsing. Degreasing, brushing and rinsing are all carried out at 55°C. Degreasing and scrubbing are carried out with lye with a concentration of 2%, and a flow production line is used for rinsing. , the production line speed is controlled at 60m / min;
[0025] Step 3: Trim the pretreated substrate, including testing the flatness of the substrate and grinding the edge of the substrate. When the flatness is tested, the qualified range of the flatness of the substrate is 0-0.6mm. When it exceeds the range of 0-0.6mm, it is necessary to continue to level the substrate until the flatness of the substrate meets the requirement...
Embodiment 2
[0030] This embodiment proposes a method for laminating a television backplane, comprising the following steps:
[0031] Step 1: Select the steel with steel quality requirements of DX53D+Z and above, and the surface requirements of FB grade and above quality standards as the substrate;
[0032] Step 2: Pretreat the substrate, including degreasing, brushing and rinsing. Degreasing, brushing and rinsing are all carried out at 55°C. Degreasing and scrubbing are carried out with lye with a concentration of 2%, and a flow production line is used for rinsing. , the production line speed is controlled at 60m / min;
[0033] Step 3: Trim the pretreated substrate, including testing the flatness of the substrate and grinding the edge of the substrate. When the flatness is tested, the qualified range of the flatness of the substrate is 0-0.6mm. When it exceeds the range of 0-0.6mm, it is necessary to continue to level the substrate until the flatness of the substrate meets the requirement...
Embodiment 3
[0038] This embodiment proposes a method for laminating a television backplane, comprising the following steps:
[0039] Step 1: Select the steel with steel quality requirements of DX53D+Z and above, and the surface requirements of FB grade and above quality standards as the substrate;
[0040] Step 2: Pretreat the substrate, including degreasing, brushing and rinsing. Degreasing, brushing and rinsing are all carried out at 55°C. Degreasing and scrubbing are carried out with lye with a concentration of 2%, and a flow production line is used for rinsing. , the production line speed is controlled at 60m / min;
[0041] Step 3: Trim the pretreated substrate, including testing the flatness of the substrate and grinding the edge of the substrate. When the flatness is tested, the qualified range of the flatness of the substrate is 0-0.6mm. When it exceeds the range of 0-0.6mm, it is necessary to continue to level the substrate until the flatness of the substrate meets the requirement...
PUM
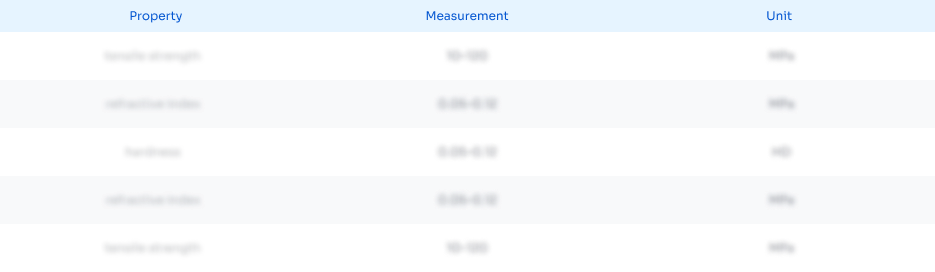
Abstract
Description
Claims
Application Information

- R&D Engineer
- R&D Manager
- IP Professional
- Industry Leading Data Capabilities
- Powerful AI technology
- Patent DNA Extraction
Browse by: Latest US Patents, China's latest patents, Technical Efficacy Thesaurus, Application Domain, Technology Topic, Popular Technical Reports.
© 2024 PatSnap. All rights reserved.Legal|Privacy policy|Modern Slavery Act Transparency Statement|Sitemap|About US| Contact US: help@patsnap.com