Method of reducing friction coefficient of coating through micro sand blasting after-treatment
A friction coefficient and coating technology, applied in the field of micro-blasting post-treatment to reduce the coating friction coefficient, can solve the problems of coating damage and performance degradation, and achieve the improvement of flatness, reduce friction coefficient, and improve anti-diffusion performance. Effect
- Summary
- Abstract
- Description
- Claims
- Application Information
AI Technical Summary
Problems solved by technology
Method used
Image
Examples
Embodiment 1
[0031] (1) Sample pretreatment: Put the deposited coating samples into acetone and ethanol for ultrasonic cleaning for 15 minutes respectively to remove surface oil and water stains.
[0032] (2) Clamping into the furnace: evenly fix the treated samples on the turntable, and put them into the arc ion coating machine.
[0033] (3) Heating and vacuuming: pump the vacuum in the furnace chamber to 7×10^3Pa, and raise the temperature to 300°C.
[0034] (4) Deposit oxide coating: deposit a thin layer of Al on the surface of the sample 2 o 3 coating;
[0035] (5) Post-treatment of micro-sandblasting on the coated blade: after the coating is deposited, lower the temperature, take out the sample after cooling, and perform post-treatment of micro-sandblasting on the sample that has deposited the coating. 600#Al for sandblasting 2 o 3 Sand, the pressure is 2kg, and the manual dry spraying time is 25s. (For specific experimental data curves, see figure 2 B curve)
Embodiment 2
[0037] (1) Sample pretreatment: Put the deposited coating samples into acetone and ethanol for ultrasonic cleaning for 15 minutes respectively to remove surface oil and water stains.
[0038] (2) Clamping into the furnace: evenly fix the treated samples on the turntable, and put them into the arc ion coating machine.
[0039] (3) Heating and vacuuming: pump the vacuum in the furnace chamber to 7×10^4Pa, and raise the temperature to 400°C.
[0040] (4) Deposit oxide coating: deposit a thin layer of TiAlO on the surface of the sample 2 coating;
[0041] (5) Post-treatment of micro-sandblasting on the coated blade: after the coating is deposited, lower the temperature, take out the sample after cooling, and perform post-treatment of micro-sandblasting on the sample that has deposited the coating. 600#Al for sandblasting 2 o 3 Sand, the pressure is 4kg, and the manual dry spraying time is 15s. (For specific experimental data curves, see figure 2 C curve)
Embodiment 3
[0043] (1) Sample pretreatment: Put the deposited coating samples into acetone and ethanol for 20min ultrasonic cleaning to remove surface oil and water stains.
[0044] (2) Clamping into the furnace: evenly fix the treated samples on the turntable, and put them into the arc ion coating machine.
[0045] (3) Heating and vacuuming: pump the vacuum in the furnace chamber to 7×10^4Pa, and raise the temperature to 400°C.
[0046] (4) Deposit oxide coating: deposit a thin layer of TiAlO on the surface of the sample 2 coating;
[0047] (5) Post-treatment of micro-sandblasting on the coated blade: after the coating is deposited, lower the temperature, take out the sample after cooling, and perform post-treatment of micro-sandblasting on the sample that has deposited the coating. 800#Al for sandblasting 2 o 3 Sand, the pressure is 4kg, and the manual dry spraying time is 10s. (For specific experimental data curves, see figure 2 D curve)
[0048] Such as figure 1 Shown is the...
PUM
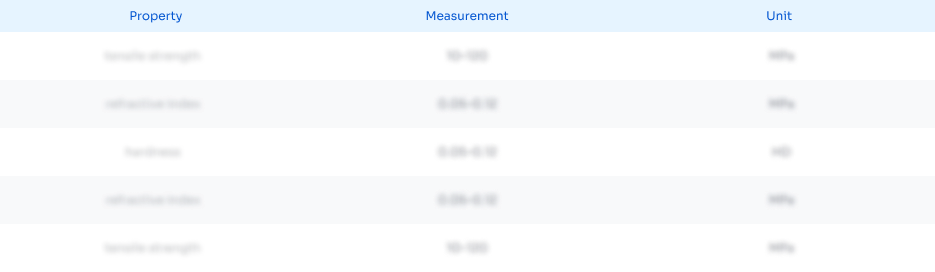
Abstract
Description
Claims
Application Information

- R&D
- Intellectual Property
- Life Sciences
- Materials
- Tech Scout
- Unparalleled Data Quality
- Higher Quality Content
- 60% Fewer Hallucinations
Browse by: Latest US Patents, China's latest patents, Technical Efficacy Thesaurus, Application Domain, Technology Topic, Popular Technical Reports.
© 2025 PatSnap. All rights reserved.Legal|Privacy policy|Modern Slavery Act Transparency Statement|Sitemap|About US| Contact US: help@patsnap.com