Main shaft and workpiece vibration prediction method based on stack sparse automatic coding network
A technology of sparse automatic coding and prediction method, which is applied in the field of spindle and workpiece vibration prediction based on stacked sparse automatic coding network, can solve the problems of complex analysis and calculation process and the influence of missing frequency response, so as to improve processing efficiency, save cost, Improvement of machining accuracy and surface quality
- Summary
- Abstract
- Description
- Claims
- Application Information
AI Technical Summary
Problems solved by technology
Method used
Image
Examples
specific Embodiment
[0070] As used in this example Figure 6 For the thin-walled part shown, the cutting experiment is carried out to obtain relevant parameters, and the prediction model is obtained by training according to the above method, and then the input data in the test set are input into the prediction model. The prediction results are as follows: Figure 3(a) ~ Figure 3(f) As shown, the fitting effect of the spindle vibration in the x direction, y direction, and z direction and the workpiece vibration in the y direction and z direction is better (the tool feed direction is the x direction, and the vertical direction is the z direction), which can be more accurate Reflect the vibration situation and trend of the spindle and workpiece during the cutting process; such as Figure 4(a) ~ Figure 4(f) It can be seen that the predicted results of the predicted data in the selected frequency band are very similar to the frequency distribution of the actual data in this frequency band, which can m...
PUM
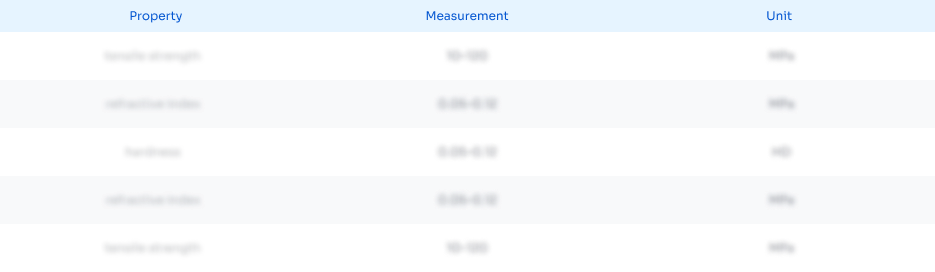
Abstract
Description
Claims
Application Information

- R&D
- Intellectual Property
- Life Sciences
- Materials
- Tech Scout
- Unparalleled Data Quality
- Higher Quality Content
- 60% Fewer Hallucinations
Browse by: Latest US Patents, China's latest patents, Technical Efficacy Thesaurus, Application Domain, Technology Topic, Popular Technical Reports.
© 2025 PatSnap. All rights reserved.Legal|Privacy policy|Modern Slavery Act Transparency Statement|Sitemap|About US| Contact US: help@patsnap.com