Gas-phase SO3 sulfonation process and production system
A production system and sulfonation technology, applied in the field of gas-phase SO3 sulfonation process and related production systems, can solve problems such as inapplicability and affecting product quality, and achieve the effects of reducing sulfur consumption, reducing equipment investment, and good environmental effects
- Summary
- Abstract
- Description
- Claims
- Application Information
AI Technical Summary
Problems solved by technology
Method used
Image
Examples
Embodiment 1
[0033] After sulfonation, the tail gas after gas-liquid separation is mixed with the oxygen input to the system, and then enters the sulfur furnace through the Roots blower; the oxygen amount is adjusted to control the oxygen concentration of the mixed gas entering the sulfur furnace to 22%.
[0034] At the same time, liquid sulfur enters the sulfur burning furnace at a flow rate of 400kg / h, contacts and burns in the sulfur burning furnace, adjusts the frequency of the Roots blower, and controls the burning sulfur temperature to 650℃. SO produced by combustion 2 The gas, according to the conventional process, is converted by the conversion tower and cooled by the cooler, SO 3 The filter finally obtains SO with a temperature of 60℃ 3 The gas enters the falling film sulfonation reactor; at the same time, dodecylbenzene enters the sulfonator at a flow rate of 2700kg / h, and is combined with SO 3 The gas contact performs the sulfonation reaction.
[0035] Maintain SO at the gas inlet of ...
Embodiment 2
[0042] After sulfonation, the tail gas after gas-liquid separation is mixed with oxygen in the input system, and enters the sulfur furnace through a Roots blower; the oxygen amount is adjusted to control the oxygen concentration of the mixed gas entering the sulfur furnace to 22%.
[0043] At the same time, liquid sulfur enters the sulfur-burning furnace at a flow rate of 300kg / h, and contacts and burns in the sulfur-burning furnace; adjusts the frequency of the Roots blower to control the sulfur combustion temperature at 650℃. SO produced by combustion 2 The gas, according to the conventional process, is converted by the conversion tower and cooled by the cooler, SO 3 The filter finally obtains SO with a temperature of 55℃ 3 The gas enters the falling film sulfonation reactor; at the same time, the fatty alcohol polyoxyethylene ether enters the sulfonator at a flow rate of 2500kg / h, and is combined with SO 3 The gas contact performs the sulfonation reaction.
[0044] Maintain SO at...
Embodiment 3
[0051] After sulfonation, the tail gas after gas-liquid separation is mixed with the oxygen input to the system, and enters the sulfur furnace through the Roots blower; the oxygen amount is adjusted to control the oxygen concentration of the mixed gas entering the sulfur furnace to 22%.
[0052] At the same time, liquid sulfur enters the sulfur burning furnace at a flow rate of 280kg / h, contacts and burns in the sulfur burning furnace, adjusts the frequency of the Roots blower, and controls the sulfur burning temperature to 600°C. SO produced by combustion 2 The gas, according to the conventional process, is converted by the conversion tower and cooled by the cooler, SO 3 The filter finally obtains SO with a temperature of 55℃ 3 The gas enters the falling film sulfonation reactor; at the same time, the alpha olefin enters the sulfonator at a flow rate of 1700kg / h, and the SO 3 The gas contact performs the sulfonation reaction.
[0053] Maintain SO at the gas inlet of the sulfonator ...
PUM
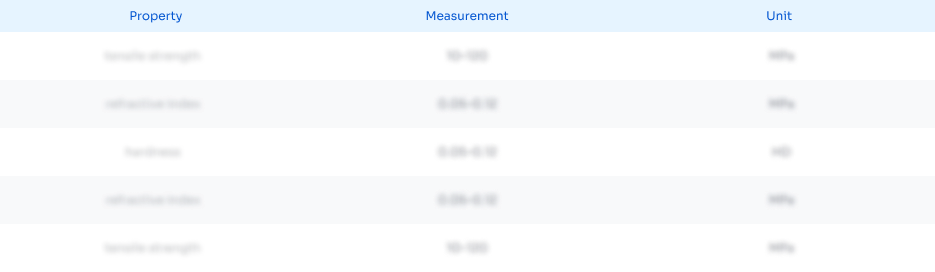
Abstract
Description
Claims
Application Information

- R&D Engineer
- R&D Manager
- IP Professional
- Industry Leading Data Capabilities
- Powerful AI technology
- Patent DNA Extraction
Browse by: Latest US Patents, China's latest patents, Technical Efficacy Thesaurus, Application Domain, Technology Topic, Popular Technical Reports.
© 2024 PatSnap. All rights reserved.Legal|Privacy policy|Modern Slavery Act Transparency Statement|Sitemap|About US| Contact US: help@patsnap.com