Grain structure numerical prediction method in metal rapid prototyping process
A metal rapid prototyping and numerical prediction technology, applied in the direction of process efficiency improvement, energy efficiency improvement, additive manufacturing, etc., can solve problems such as large amount of calculation, achieve optimization of process, huge market application potential, and accurately predict grain structure. Effect
- Summary
- Abstract
- Description
- Claims
- Application Information
AI Technical Summary
Problems solved by technology
Method used
Image
Examples
Embodiment 1
[0283] Example 1: Such as figure 2 As shown, the Z axis is the direction of gravity, and the X axis is the direction of laser migration. The label "①" represents the substrate, the label "③" represents the molten pool, and the label "②" represents the epitaxial crystal grain nucleation area. In the direct energy deposition process, the substrate is heated to melt and then solidifies. The formed molten pool is not rectangular, and the morphology of the molten pool is related to the physical properties of the alloy itself and process parameters. Such as figure 2 As shown in (c), the depth of substrate melting (H e ) Will affect the bonding strength between the melt channel above the substrate and the substrate, H e The larger the bond strength will increase. figure 2 (d) is the central cross section perpendicular to the Y axis. It can be seen that a continuous molten pool is formed in the substrate, thus ensuring the continuity of the structure and the uniformity of mechanical...
Embodiment 2
[0286] Example 2: Such as image 3 As shown, the Z axis is the direction of gravity, and the X axis is the direction of laser migration. The label "①" represents the substrate, the label "③" represents the molten pool, and the label "②" represents the epitaxial crystal grain nucleation area. In this embodiment, the viscosity of the liquid is high, and the molten metal basically does not flow. Some existing studies generally assume that the liquid does not flow to simplify calculations. Compared image 3 (c) and figure 2 (c) It can be seen that due to image 3 There is no liquid flowing in it, so the formed molten pool is narrower and the molten channel above the substrate is higher. image 3 (d) is the central section perpendicular to the Y axis, contrast image 3 (d) and figure 2 (d) It can be seen that in image 3 (d) There is a tiny area (wire frame) above the middle substrate, which is formed by metal powder that is not completely melted, which destroys the connectivity be...
PUM
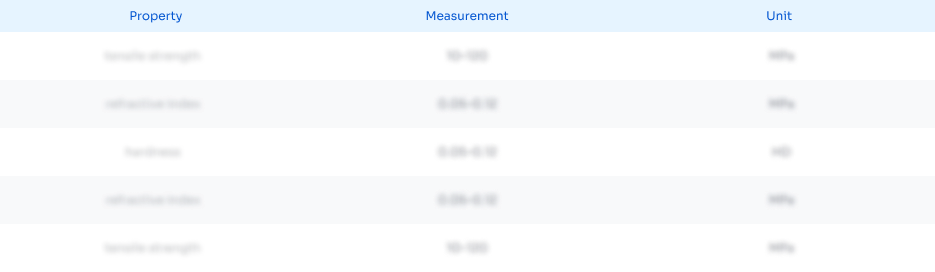
Abstract
Description
Claims
Application Information

- R&D
- Intellectual Property
- Life Sciences
- Materials
- Tech Scout
- Unparalleled Data Quality
- Higher Quality Content
- 60% Fewer Hallucinations
Browse by: Latest US Patents, China's latest patents, Technical Efficacy Thesaurus, Application Domain, Technology Topic, Popular Technical Reports.
© 2025 PatSnap. All rights reserved.Legal|Privacy policy|Modern Slavery Act Transparency Statement|Sitemap|About US| Contact US: help@patsnap.com