Production method, obtained product and application of microcrystalline mullite-type calcined kaolin
A technology for calcining kaolin and microcrystalline mullite, which is applied in the production of microcrystalline mullite type calcined kaolin and in the field of microcrystalline mullite type calcined kaolin, can solve the problem that the quality of calcined kaolin is poor and the high whiteness calcined kaolin cannot be applied. High-speed rail raw materials, limited applications, etc., to achieve the effect of facilitating air circulation, increasing effective space, and improving economic benefits
- Summary
- Abstract
- Description
- Claims
- Application Information
AI Technical Summary
Problems solved by technology
Method used
Image
Examples
Embodiment 1
[0046] The composition of high-speed iron coal gangue raw materials (the content is calculated after calcination, the same below) is shown in the following table 1:
[0047] SiO 2
Al 2 o 3
Fe 2 o 3
TiO 2
other 54.1% 43.2% 0.8% 1.1% 0.8%
[0048] 1) As can be seen from Table 1, Al in the raw material 2 o 3 Greater than 30%, Fe 2 o 3 Greater than 0.4%, no need to add aluminum regulator,
[0049] 2) Crushing the raw materials obtained in step 1) and grinding them to 100 mesh to obtain a mixed powder,
[0050] 3) Add water to the mixed powder and mix evenly to make a wet material. The weight ratio of the mixed powder to water is 75:25, and the water content of the wet material is 25%. The wet material is aged for 8 hours and squeezed to make The bricks are stacked on the kiln car and dried until the moisture is less than 5%. After drying, the kiln car enters the tunnel kiln for calcination. The temperature in the tunnel kiln i...
Embodiment 2
[0052] The composition of high-speed rail coal gangue raw materials is shown in Table 2 below:
[0053] SiO 2
Al 2 o 3
Fe 2 o 3
TiO 2
other 70.1% 27.2% 0.7% 1.3% 0.7%
[0054] 1) As can be seen from Table 2, Al in the raw material 2 o 3 Less than 30%, Fe 2 o 3 More than 0.4%, add bauxite to adjust Al 2 o 3 content to 32%,
[0055] 2) Crushing the raw materials obtained in step 1), grinding them to 150 mesh to obtain a mixed powder,
[0056] 3) Add water to the mixed powder and mix evenly to make a wet material. The weight ratio of the mixed powder to water is 90:10, and the water content of the wet material is 10%. The wet material is aged for 4 hours and squeezed to make The bricks are stacked on the kiln car and dried until the moisture is less than 5%. After drying, the kiln car enters the tunnel kiln for calcination. The temperature in the tunnel kiln is below 1100°C, it is an oxidizing atmosphere, and when it is above...
Embodiment 3
[0058] The composition of high-speed rail coal gangue raw materials is shown in Table 3 below:
[0059] SiO 2
al 2 o 3
Fe 2 o 3
TiO 2
other 68.8 28.5% 1.0% 0.9% 0.8%
[0060] 1) As can be seen from Table 3, Al in raw materials 2 o 3 Less than 30%, Fe 2 o 3 More than 0.4%, add aluminum powder to adjust Al 2 o 3 content to 38%,
[0061] 2) Crushing the raw materials obtained in step 1), grinding them to 150 mesh to obtain a mixed powder,
[0062] 3) Add water to the mixed powder and mix evenly to make a wet material. The weight ratio of the mixed powder to water is 80:20. The water content of the wet material is 20%. The wet material is aged for 2 hours and squeezed to make The bricks are stacked on the kiln car and dried until the moisture is less than 5%. After drying, the kiln car enters the tunnel kiln for calcination. The temperature in the tunnel kiln is below 1100°C, it is an oxidizing atmosphere, and when it is abo...
PUM
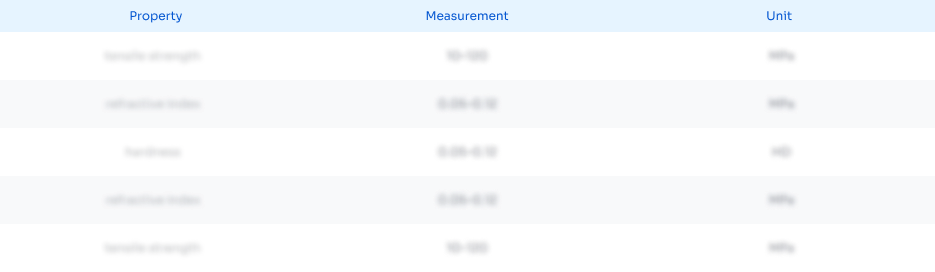
Abstract
Description
Claims
Application Information

- R&D
- Intellectual Property
- Life Sciences
- Materials
- Tech Scout
- Unparalleled Data Quality
- Higher Quality Content
- 60% Fewer Hallucinations
Browse by: Latest US Patents, China's latest patents, Technical Efficacy Thesaurus, Application Domain, Technology Topic, Popular Technical Reports.
© 2025 PatSnap. All rights reserved.Legal|Privacy policy|Modern Slavery Act Transparency Statement|Sitemap|About US| Contact US: help@patsnap.com