Hydraulic telescopic cutter and differential mechanism shell machining method applying the same
A differential housing and hydraulic technology, applied in metal processing equipment, metal processing machinery parts, manufacturing tools, etc., can solve problems such as high requirements, high price, and difficult processing, so as to reduce position accuracy deviation and reduce investment Cost, the effect of reducing investment risk
- Summary
- Abstract
- Description
- Claims
- Application Information
AI Technical Summary
Problems solved by technology
Method used
Image
Examples
Embodiment Construction
[0021] Such as Figure 1-3 As shown, the present invention provides a technical solution: a hydraulic retractable tool, including a turret 1, a differential case 2, a hinge shaft 3, a connecting rod 4, a tool bar 6, a fixed sleeve 7, a working chamber 8, The end face automatic knife 11, the tool telescopic control connecting rod 12, the tool telescopic hydraulic cylinder 13, the gasket 14 and the ball cage knife 15, the inner wall of the turret 1 is fixedly connected with the outer wall of the working chamber 8, and the outer wall of the fixed sleeve 7 is connected with the working chamber 8 The outer wall of the tool telescopic hydraulic cylinder 13 is fixedly connected to the right side of the tool telescopic control connecting rod 12, the outer surface of the tool telescopic control connecting rod 12 is flexibly connected to the inner wall of the gasket 14, and the tool telescopic control connecting rod The left side of 12 is fixedly connected with the right side of knife b...
PUM
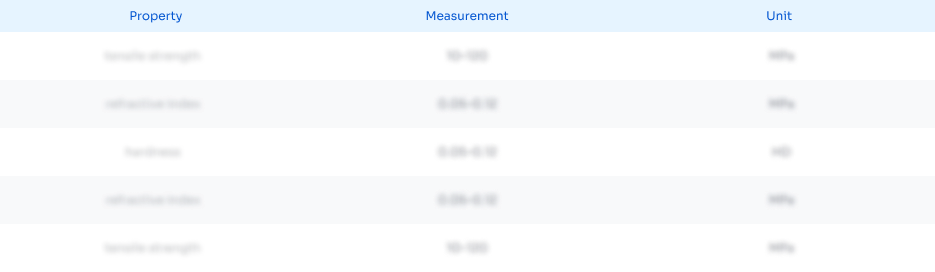
Abstract
Description
Claims
Application Information

- Generate Ideas
- Intellectual Property
- Life Sciences
- Materials
- Tech Scout
- Unparalleled Data Quality
- Higher Quality Content
- 60% Fewer Hallucinations
Browse by: Latest US Patents, China's latest patents, Technical Efficacy Thesaurus, Application Domain, Technology Topic, Popular Technical Reports.
© 2025 PatSnap. All rights reserved.Legal|Privacy policy|Modern Slavery Act Transparency Statement|Sitemap|About US| Contact US: help@patsnap.com