High-temperature spiral feeder
A screw feeder and high-temperature technology, which is applied in the field of material conveying equipment, can solve the problems of wasting water resources, complex water seal of the rotating shaft, and high operating costs, and achieve energy saving, simple and compact overall structure, and low operating costs.
- Summary
- Abstract
- Description
- Claims
- Application Information
AI Technical Summary
Problems solved by technology
Method used
Image
Examples
Embodiment Construction
[0020] Such as figure 1 As shown, a high-temperature screw feeder of the present invention includes a motor reducer 23 , a cooling section 24 , a heat insulation section 25 and a high-temperature feeding section 26 connected in sequence from left to right. The output shaft 18 of the motor reducer 23 passes through the cooling section 24 and then connects with the auger main shaft 4 in the high temperature feeding section 26 through the coupling 16 in the heat insulation section 25 .
[0021] combine figure 2 Shown:
[0022] The main function of the cooling section 24 is to absorb the heat transferred from the high-temperature feeding section 26 through the heat insulation section 25 by means of refrigeration, and to control the temperature of the cooling section 24 and the output shaft 18 at about room temperature. The cooling section 24 includes a cooling box 20, a temperature sensor 29 arranged in the inner cavity of the cooling box 20, a semiconductor refrigerator 21 arr...
PUM
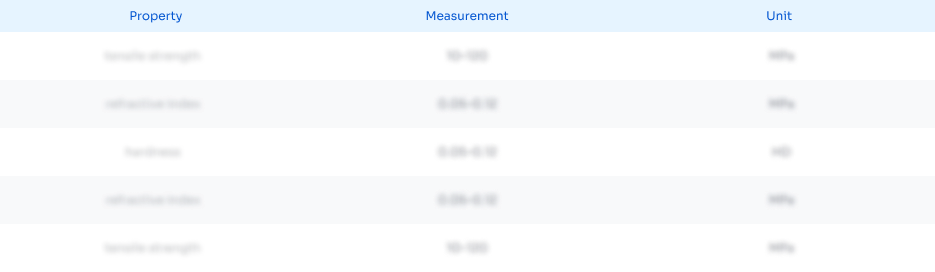
Abstract
Description
Claims
Application Information

- R&D
- Intellectual Property
- Life Sciences
- Materials
- Tech Scout
- Unparalleled Data Quality
- Higher Quality Content
- 60% Fewer Hallucinations
Browse by: Latest US Patents, China's latest patents, Technical Efficacy Thesaurus, Application Domain, Technology Topic, Popular Technical Reports.
© 2025 PatSnap. All rights reserved.Legal|Privacy policy|Modern Slavery Act Transparency Statement|Sitemap|About US| Contact US: help@patsnap.com