A permanent magnet servo system for cleaning dust particles and reducing vibration frequency
A vibration frequency, servo system technology, applied in the field of servo systems, can solve the problems of reduced accuracy of operating data, increased frequency of collisions, abnormal operation of equipment, etc., to achieve the effect of improving stability, reducing vibration frequency and stable operation of equipment
- Summary
- Abstract
- Description
- Claims
- Application Information
AI Technical Summary
Problems solved by technology
Method used
Image
Examples
Embodiment 1
[0031] Example 1 see Figure 1-6 , the present invention provides a permanent magnet servo system technical solution for cleaning dust particles and reducing vibration frequency: its structure includes a drill bit 1, a fuselage 2, a machine board 3, a control ring 4, and a machine cover 5, and the machine board 3 strengthens the The improvement of the stability of the operation of the fuselage 2, the drill bit 1 is locked with the fuselage 2, the fuselage 2 is welded with the machine plate 3, the control ring 4 is installed on the fuselage 2, and the fuselage 2 is connected with the fuselage 2. The hood 5 is installed and connected. The control ring 4 is composed of a square buckle 40, a button 41 and a ring belt 42. The square buckle 40 and the button 41 are embedded in the ring belt 42. The button 41 is used to adjust the ring The elastic variation of belt 42, square buckle 40 are used to adjust the movement of endless belt 42 and strengthen the fixation to machine cover 5, ...
Embodiment 2
[0033] Example 2 see Figure 7-11 , the present invention provides a permanent magnet servo system technical solution for cleaning dust particles and reducing vibration frequency: the drill pipe 12 in its structure includes a slit rod 120, a strip ring 121, an arc dividing plate 122, and a bottom circle structure 123, and the slit The rod 120 is connected to the arc dividing plate 122 track, the strip ring 121 is installed and connected with the seam bar 120 and the arc dividing plate 122, and the arc dividing plate 122 is installed and connected with the bottom circle structure 123, and the bottom circle structure 123 acts on After the particles enter the drill pipe 12, they act as a buffer to realize the slow feeding and orderly feeding of the particles. The particles are concentrated at the slitting ring 121 to facilitate later cleaning and ensure the stability of the drill pipe 12 rotation. The bottom circle structure 123 comprises a bottom circle shaft rod 1230, a bottom ...
PUM
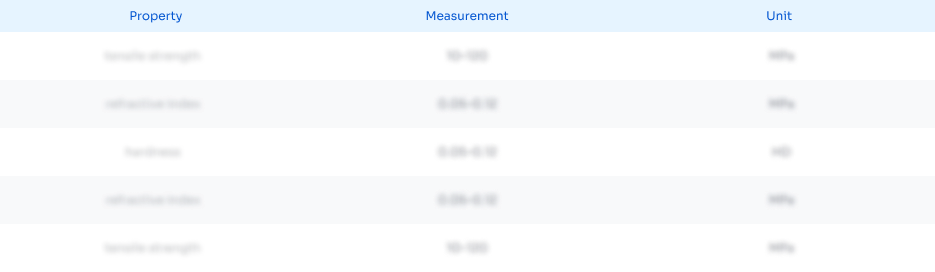
Abstract
Description
Claims
Application Information

- Generate Ideas
- Intellectual Property
- Life Sciences
- Materials
- Tech Scout
- Unparalleled Data Quality
- Higher Quality Content
- 60% Fewer Hallucinations
Browse by: Latest US Patents, China's latest patents, Technical Efficacy Thesaurus, Application Domain, Technology Topic, Popular Technical Reports.
© 2025 PatSnap. All rights reserved.Legal|Privacy policy|Modern Slavery Act Transparency Statement|Sitemap|About US| Contact US: help@patsnap.com