A wide temperature range ni with cu@ni core-shell structure as lubricating phase 3 Al-based self-lubricating composite material and preparation method thereof
A core-shell structure and composite material technology, applied in metal processing equipment, transportation and packaging, etc., can solve the problems of limited service life of coatings, reduced mechanical properties of materials, restricted application, etc., achieve good compactness, improve synthesis efficiency, The effect of saving synthesis cost
- Summary
- Abstract
- Description
- Claims
- Application Information
AI Technical Summary
Problems solved by technology
Method used
Image
Examples
Embodiment 1
[0026] A wide temperature range Ni with Cu@Ni core-shell structure as the lubricating phase 3 Al-based self-lubricating composite materials, the weight composition of its raw materials are: respectively according to Ni 3 10wt.% and 10wt.% of the total mass of Al alloy powder are selected from the above-mentioned Cu@Ni powder and Mo powder; wherein Ni 3 Al is made of Ni powder and Al powder with a molar ratio of Ni:Al=3:1. Sample number NA10.
[0027] The preparation process steps of this example are as follows:
[0028] Step 1. First, the purity is greater than or equal to 95%, and the 200-300 mesh Ni powder and Al powder are weighed according to the following ratio, and the molar ratio Ni:Al=3:1.
[0029] Step 2. Put the ingredients obtained in step 1 into a zirconia ball mill tank for mechanical alloying. The ball milling speed is 200rpm, the continuous ball milling time is 35 hours, the mass ratio of balls to materials is 10:1, and the ball milling process control agent ...
Embodiment 2
[0036] A wide temperature range Ni with Cu@Ni core-shell structure as the lubricating phase 3 Al-based self-lubricating composite materials, the weight composition of its raw materials are: respectively according to Ni 3 10wt.% and 10wt.% of the total mass of Al alloy powder are selected from the above-mentioned Cu@Ni powder and Mo powder; wherein Ni 3 Al is made of Ni powder and Al powder with a molar ratio of Ni:Al=3:1. Sample number NA15.
[0037] The preparation process steps of this example are as follows:
[0038] Step 1. First, the purity is greater than or equal to 95%, and the 200-300 mesh Ni powder and Al powder are weighed according to the following ratio, and the molar ratio Ni:Al=3:1.
[0039]Step 2. Put the ingredients obtained in step 1 into a zirconia ball mill tank for mechanical alloying. The ball milling speed is 200rpm, the continuous ball milling time is 35 hours, the mass ratio of balls to materials is 10:1, and the ball milling process control agent i...
Embodiment 3
[0047] A wide temperature range Ni with Cu@Ni core-shell structure as the lubricating phase 3 Al-based self-lubricating composite materials, the weight composition of its raw materials are: respectively according to Ni 3 10wt.% and 10wt.% of the total mass of Al alloy powder are selected from the above-mentioned Cu@Ni powder and Mo powder; wherein Ni 3 Al is made of Ni powder and Al powder with a molar ratio of Ni:Al=3:1. Sample number NA20.
[0048] The preparation process steps of this example are as follows:
[0049] Step 1. First, the purity is greater than or equal to 95%, and the 200-300 mesh Ni powder and Al powder are weighed according to the following ratio, and the molar ratio Ni:Al=3:1.
[0050] Step 2. Put the ingredients obtained in step 1 into a zirconia ball mill tank for mechanical alloying. The ball milling speed is 200rpm, the continuous ball milling time is 35 hours, the mass ratio of balls to materials is 10:1, and the ball milling process control agent ...
PUM
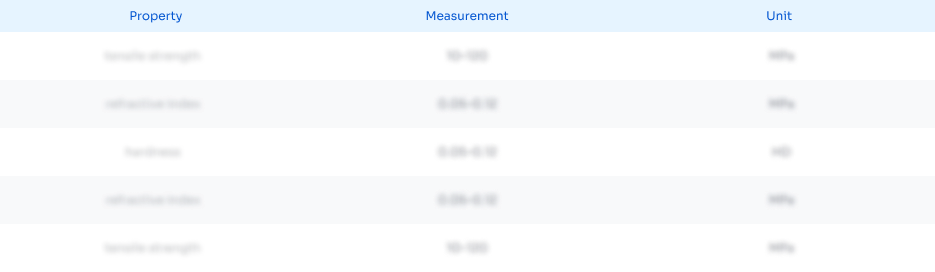
Abstract
Description
Claims
Application Information

- R&D
- Intellectual Property
- Life Sciences
- Materials
- Tech Scout
- Unparalleled Data Quality
- Higher Quality Content
- 60% Fewer Hallucinations
Browse by: Latest US Patents, China's latest patents, Technical Efficacy Thesaurus, Application Domain, Technology Topic, Popular Technical Reports.
© 2025 PatSnap. All rights reserved.Legal|Privacy policy|Modern Slavery Act Transparency Statement|Sitemap|About US| Contact US: help@patsnap.com