Concrete for cast-in-place pile, and preparation method thereof
A technology for concrete and flocculant, applied in the field of concrete, can solve the problems of material formulation and construction technology not meeting requirements, increasing demand for high-quality concrete, and reducing concrete workability, etc., to achieve good dispersion resistance, provide workability, concrete good workability
- Summary
- Abstract
- Description
- Claims
- Application Information
AI Technical Summary
Problems solved by technology
Method used
Image
Examples
Embodiment 1
[0036] A concrete for cast-in-situ piles, comprising the following raw materials in parts by weight: 280 parts of cement, 350 parts of sand, 450 parts of stones, 5 parts of anti-corrosion and rust inhibitors, 6 parts of flocculants, 5 parts of water reducing agents and 115 parts of water,
[0037] Wherein, the water reducer is a polycarboxylate water reducer,
[0038] The mass ratio of hydroxymethylcellulose, polyacrylamide and chitosan in the flocculant is 5:3:1;
[0039] The anticorrosion and rust inhibitor includes the following components by weight:
[0040] 16 parts of calcium nitrite, 10 parts of calcium oxide, 5 parts of cyclodextrin, 42 parts of fly ash and 10 parts of sodium silicate.
[0041] The above-mentioned preparation method for the concrete of cast-in-place pile comprises the following steps:
[0042] (1) Mix and grind hydroxymethyl cellulose, polyacrylamide, chitosan, calcium nitrite, fly ash, calcium oxide, cyclodextrin and water reducing agent with diatom...
Embodiment 2
[0047] A concrete for cast-in-place piles, comprising the following raw materials in parts by weight: 300 parts of cement, 480 parts of sand, 540 parts of stones, 9 parts of anti-corrosion and rust inhibitors, 10 parts of flocculants, 7 parts of water reducing agents and 140 parts of water,
[0048] Wherein, the water reducer is a polycarboxylate water reducer,
[0049]The mass ratio of hydroxymethylcellulose, polyacrylamide and chitosan in the flocculant is 6:1:1;
[0050] The anticorrosion and rust inhibitor includes the following components by weight:
[0051] 18 parts of calcium nitrite, 20 parts of calcium oxide, 9 parts of cyclodextrin, 50 parts of fly ash and 13 parts of sodium silicate.
[0052] The above-mentioned preparation method for the concrete of cast-in-place pile comprises the following steps:
[0053] (1) Mix and grind hydroxymethyl cellulose, polyacrylamide, chitosan, calcium nitrite, fly ash, calcium oxide, cyclodextrin and water reducing agent with diato...
Embodiment 3
[0058] A concrete for cast-in-situ piles, comprising the following raw materials in parts by weight: 290 parts of cement, 400 parts of sand, 500 parts of stones, 7 parts of anti-corrosion and rust inhibitors, 8 parts of flocculants, 6 parts of water reducing agents and 125 parts of water,
[0059] Wherein, the water reducer is a polycarboxylate water reducer,
[0060] The mass ratio of hydroxymethylcellulose, polyacrylamide and chitosan in the flocculant is 4:2:1;
[0061] The anticorrosion and rust inhibitor includes the following components by weight:
[0062] 17 parts of calcium nitrite, 15 parts of calcium oxide, 7 parts of cyclodextrin, 46 parts of fly ash and 12 parts of sodium silicate.
[0063] The above-mentioned preparation method for the concrete of cast-in-place pile comprises the following steps:
[0064] (1) Mix and grind hydroxymethyl cellulose, polyacrylamide, chitosan, calcium nitrite, fly ash, calcium oxide, cyclodextrin and water reducing agent with diatom...
PUM
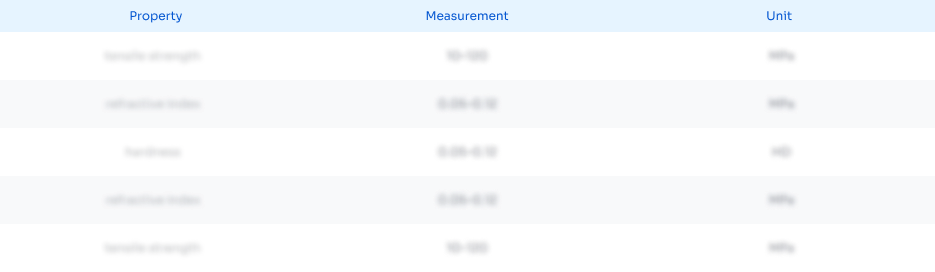
Abstract
Description
Claims
Application Information

- R&D Engineer
- R&D Manager
- IP Professional
- Industry Leading Data Capabilities
- Powerful AI technology
- Patent DNA Extraction
Browse by: Latest US Patents, China's latest patents, Technical Efficacy Thesaurus, Application Domain, Technology Topic, Popular Technical Reports.
© 2024 PatSnap. All rights reserved.Legal|Privacy policy|Modern Slavery Act Transparency Statement|Sitemap|About US| Contact US: help@patsnap.com