Automobile A-pillar manufacturing method
A manufacturing method and automobile technology, applied to vehicle components, superstructures, subassemblies of superstructures, etc., can solve the problems of enlarging the driver's blind spot, high cost, and enlarged cross-sectional area, so as to reduce the blind spot of vision and lighten the Weight, driving safety improvement effect
- Summary
- Abstract
- Description
- Claims
- Application Information
AI Technical Summary
Problems solved by technology
Method used
Image
Examples
Embodiment Construction
[0020] Below in conjunction with accompanying drawing and specific embodiment the present invention is described in further detail:
[0021] The invention relates to a method for manufacturing an automobile A-pillar. Firstly, the structure of the automobile A-pillar is improved, and then the processing and manufacturing method of the automobile A-pillar is further disclosed.
[0022] like figure 1 Shown is a schematic diagram of a car, which includes a car A-pillar 1, a front windshield 2 and a side windshield 3. Both the windshield 2 and the side windshield 3 need the A-pillar 1 of the automobile to be clamped and fixed. The A-pillar 1 of the automobile includes a frame and a transparent glass material 10 embedded in the frame.
[0023] like figure 2 , image 3 , Figure 4 As shown, the framework of the automobile A-pillar 1 in the present invention includes the automobile A-pillar outer part 4 and the automobile A-pillar inner part 8 . The outer part 4 of the A-pillar...
PUM
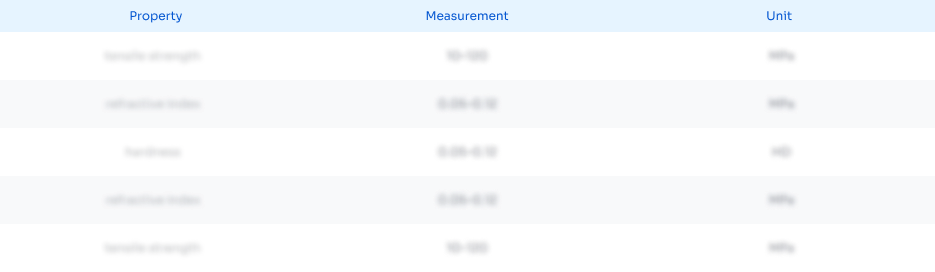
Abstract
Description
Claims
Application Information

- R&D Engineer
- R&D Manager
- IP Professional
- Industry Leading Data Capabilities
- Powerful AI technology
- Patent DNA Extraction
Browse by: Latest US Patents, China's latest patents, Technical Efficacy Thesaurus, Application Domain, Technology Topic, Popular Technical Reports.
© 2024 PatSnap. All rights reserved.Legal|Privacy policy|Modern Slavery Act Transparency Statement|Sitemap|About US| Contact US: help@patsnap.com