A kind of gh141 alloy forging forming method
A forming method and forging technology, applied in the field of forging thermal processing, can solve problems such as resource waste, unsatisfactory products, and product scrapping, and achieve the effect of improving product yield
- Summary
- Abstract
- Description
- Claims
- Application Information
AI Technical Summary
Problems solved by technology
Method used
Examples
specific Embodiment
[0051] The first level of inner ring forgings described in the present invention, part size Material: GH141, category II, process regulations require blanking specifications: Weight: 30.7Kg. The overall performance index and grain size requirements of the forgings should meet the requirements of the xx-0504 standard (grain size requirements are grade 4).
[0052]The forging steps are detailed as follows:
[0053] first step: Put the batch material into the electric furnace at 890°C for 90 minutes, heat it to 1020°C for 60 minutes, and then upset the cake to (1 fire complete); (1 fire complete);
[0054] Step 2: Car inner hole to And chamfer R10 on the upper and lower end faces of the inner hole; sand and polish.
[0055] Step 3: Put the forgings in the furnace at 890°C for 60 minutes, then raise the temperature to 1010°C for 40 minutes (3 fires are completed); expand the end face to the barren shape:
[0056] Step 4: Ream the hole in the furnace at 890°C for 50 ...
PUM
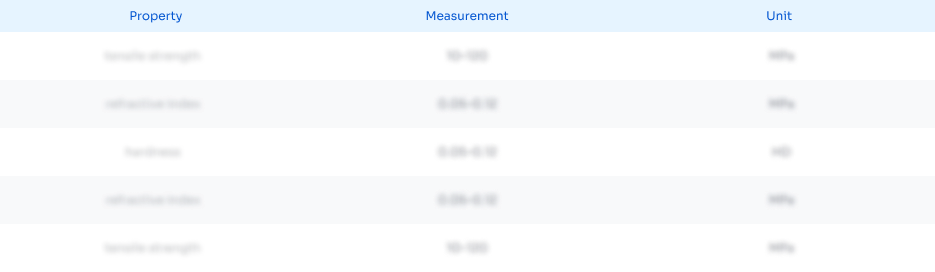
Abstract
Description
Claims
Application Information

- Generate Ideas
- Intellectual Property
- Life Sciences
- Materials
- Tech Scout
- Unparalleled Data Quality
- Higher Quality Content
- 60% Fewer Hallucinations
Browse by: Latest US Patents, China's latest patents, Technical Efficacy Thesaurus, Application Domain, Technology Topic, Popular Technical Reports.
© 2025 PatSnap. All rights reserved.Legal|Privacy policy|Modern Slavery Act Transparency Statement|Sitemap|About US| Contact US: help@patsnap.com