Composite control method for first-order inertia pure lag process
A technology of composite control and control method, applied in the direction of adaptive control, general control system, control/regulation system, etc., can solve problems such as control instability and mismatch, and achieve the effect of improving robustness
- Summary
- Abstract
- Description
- Claims
- Application Information
AI Technical Summary
Problems solved by technology
Method used
Image
Examples
Embodiment Construction
[0020] The specific embodiment of the present invention and working process will be further described below in conjunction with accompanying drawing.
[0021] The first-order inertial pure hysteresis process is a single-input and single-output link. The relationship between the controlled variable (output) Y(s) and the adjusted variable (input) U(s) can be expressed as:
[0022]
[0023] Among them, K represents the gain coefficient, T represents the time constant, and τ represents the delay time. The goal of the controller design is to make the controlled quantity of this link track the change of the set value. However, due to the perturbation in the real environment, the change of model parameters caused by the change of operating conditions, and the constraints brought by physical limitations, the performance of the controller cannot meet expectations.
[0024] The purpose of the present invention is to propose a model predictive control-ADRC composite control method fo...
PUM
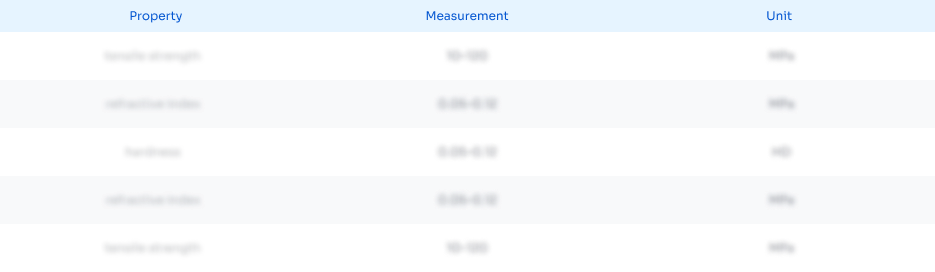
Abstract
Description
Claims
Application Information

- R&D
- Intellectual Property
- Life Sciences
- Materials
- Tech Scout
- Unparalleled Data Quality
- Higher Quality Content
- 60% Fewer Hallucinations
Browse by: Latest US Patents, China's latest patents, Technical Efficacy Thesaurus, Application Domain, Technology Topic, Popular Technical Reports.
© 2025 PatSnap. All rights reserved.Legal|Privacy policy|Modern Slavery Act Transparency Statement|Sitemap|About US| Contact US: help@patsnap.com