Process gas purging method
A process gas and process technology, applied in metal material coating process, electrical components, gaseous chemical plating, etc., can solve the problems of excessive particle size control, residual DCE in pipelines, short purge time, etc., and reduce the number of particles. , prolong the time, reduce the effect of process gas
- Summary
- Abstract
- Description
- Claims
- Application Information
AI Technical Summary
Problems solved by technology
Method used
Image
Examples
Embodiment Construction
[0032] In order to enable those skilled in the art to better understand the technical solution of the present invention, the purging method provided by the present invention will be described in detail below in conjunction with the accompanying drawings.
[0033] Such as figure 1 with figure 2 Shown, the purging method provided by the invention comprises the following steps:
[0034] S1, in the pre-process stage, before the main process of the processed workpiece, the purge gas is introduced into the intake pipeline 2 to purge the intake pipeline 2, and the purged gas directly enters the exhaust pipeline 4 ;
[0035] S2, in the post-process stage, after the processed workpiece undergoes the main process and is removed from the reaction chamber 3, a purge gas is introduced into the intake pipeline 2 to purge the intake pipeline 2 and the reaction chamber 3.
[0036] In this embodiment, the residual process gas in the intake pipeline 2 can be reduced by purging the intake pi...
PUM
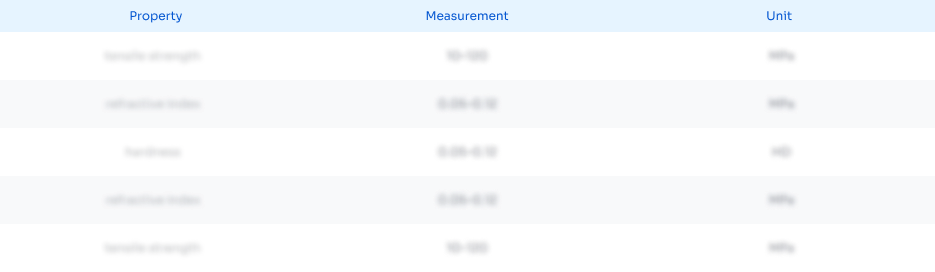
Abstract
Description
Claims
Application Information

- R&D
- Intellectual Property
- Life Sciences
- Materials
- Tech Scout
- Unparalleled Data Quality
- Higher Quality Content
- 60% Fewer Hallucinations
Browse by: Latest US Patents, China's latest patents, Technical Efficacy Thesaurus, Application Domain, Technology Topic, Popular Technical Reports.
© 2025 PatSnap. All rights reserved.Legal|Privacy policy|Modern Slavery Act Transparency Statement|Sitemap|About US| Contact US: help@patsnap.com