Method for reducing influence of robot joint structure errors on precision of robot
A technology of robot joints and robots, applied in manipulators, program-controlled manipulators, manufacturing tools, etc., can solve problems such as accuracy effects and robot joint structure errors
- Summary
- Abstract
- Description
- Claims
- Application Information
AI Technical Summary
Problems solved by technology
Method used
Image
Examples
Embodiment Construction
[0064] The present invention will be further described below in combination with specific embodiments.
[0065] A method to reduce the impact of robot joint structure errors on its accuracy:
[0066] S1. Establish the representation of the screw theory and the forward kinematics model of the robot;
[0067] The expression is: $=(s s 0 ) T =(s s 0 +hs) T =(s r×s+hs) T
[0068] Among them, s is the unit vector representing the direction of the screw axis; r is any point on the screw axis; s 0 is the dual part vector of the screw; h is the pitch;
[0069] The forward kinematics model of the robot is:
[0070]
[0071] S2. Analyze the geometric error of the joints; there is a deviation at the joint connection of the robot, that is, the theoretical axis of the joint is inconsistent with the actual axis. According to its spatial position relationship, it can be divided into: two axes are in the same plane; two axes are in different planes;
[0072] When the two axes are ...
PUM
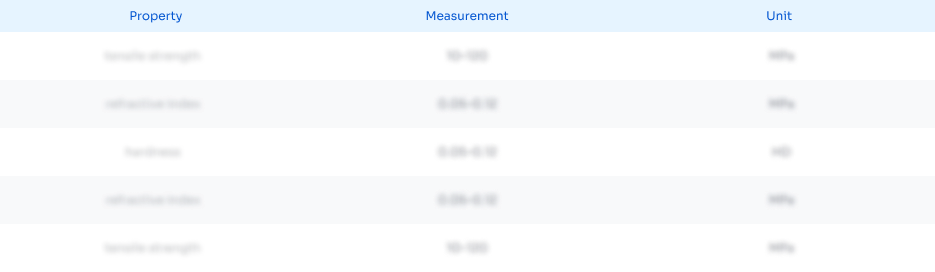
Abstract
Description
Claims
Application Information

- R&D Engineer
- R&D Manager
- IP Professional
- Industry Leading Data Capabilities
- Powerful AI technology
- Patent DNA Extraction
Browse by: Latest US Patents, China's latest patents, Technical Efficacy Thesaurus, Application Domain, Technology Topic, Popular Technical Reports.
© 2024 PatSnap. All rights reserved.Legal|Privacy policy|Modern Slavery Act Transparency Statement|Sitemap|About US| Contact US: help@patsnap.com