Method for producing abs-based graft copolymer and method for producing thermoplastic resin composition
A graft copolymer and graft polymerization technology, the disclosure content applied in the patent application is incorporated in this specification by reference. field, to achieve excellent process efficiency, excellent physical properties, and improve productivity
- Summary
- Abstract
- Description
- Claims
- Application Information
AI Technical Summary
Problems solved by technology
Method used
Image
Examples
preparation example Construction
[0029] The preparation method of the ABS graft copolymer of the present invention comprises: a first graft polymerization step, grafting 4% to 15% by weight of vinyl monomers to 20% to 70% by weight of conjugated diene rubber latex on; a latex coagulation step, after the first graft polymerization step, the particle size of the rubber latex is increased by adding a polymer coagulant; and a second graft polymerization step, after the latex coagulation step, 25 % by weight to 75% by weight of the vinyl monomer grafted onto the rubber latex with increased particle size, wherein, based on 100 parts by weight of the sum of the conjugated diene rubber latex and the vinyl monomer, The added amount of the polymer coagulant is 1 to 4 parts by weight; the vinyl monomer includes vinyl aromatic compounds and vinyl cyanide compounds; the average particle diameter of the rubber latex with increased particle diameter is to In this case, coagulation efficiency, productivity and impact resi...
preparation Embodiment 1
[0101] Preparation Example 1: Preparation of Polymer Coagulant
[0102] 208 parts by weight of distilled water and 0.75 parts by weight of dioctyl sodium sulfosuccinate (DOSS) as an emulsifier were added to the reactor, and stirred while heating to 80°C. Then, 0.2 parts by weight of potassium persulfate (KPS) as an initiator and 50 parts by weight of butyl acrylate (BA) were added to the reactor, and a reaction was performed for 90 minutes. Subsequently, 41 parts by weight of butyl acrylate and 9 parts by weight of methacrylic acid (MAA) were added and allowed to react. Finally, the average particle size is obtained as The polymer coagulant (the weight ratio of the core and the shell is 50:50, the core contains 50 parts by weight of BA, the shell contains 41 parts by weight of BA and the MAA of 9 parts by weight, and the amount of functional monomer contained in the shell is 18% by weight).
preparation Embodiment 2
[0103] Preparation Example 2: Preparation of Small Diameter Rubber Latex
[0104] Add 100 parts by weight of 1,3-butadiene, 1 to 4 parts by weight of emulsifier, 0.1 to 0.6 parts by weight of polymerization initiator, 0.1 to 1 part by weight of electrolyte, 0.1 parts by weight of 0.5 parts by weight of molecular weight modifier and 90 to 130 parts by weight of deionized water, and react at 50°C to 65°C for 7 to 12 hours. Then, 0.05 to 1.2 parts by weight of a molecular weight regulator is additionally added in batches, and reacted at 55°C to 70°C for 5 to 15 hours to obtain a small-diameter rubber latex.
PUM
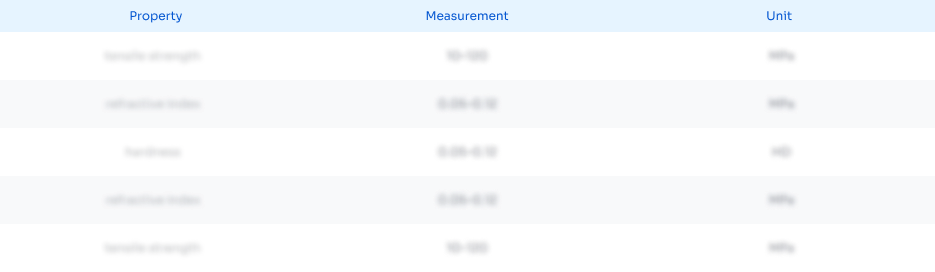
Abstract
Description
Claims
Application Information

- R&D Engineer
- R&D Manager
- IP Professional
- Industry Leading Data Capabilities
- Powerful AI technology
- Patent DNA Extraction
Browse by: Latest US Patents, China's latest patents, Technical Efficacy Thesaurus, Application Domain, Technology Topic, Popular Technical Reports.
© 2024 PatSnap. All rights reserved.Legal|Privacy policy|Modern Slavery Act Transparency Statement|Sitemap|About US| Contact US: help@patsnap.com