Ruthenium-doped moo in an acidic aqueous solution 3 Cathode material and preparation method thereof
A technology of acidic aqueous solution and cathode material, which is applied in the direction of hybrid capacitor electrodes, etc., can solve the problems of little research on batteries and difficulty in meeting voltage requirements, and achieve the effect of effective electron transfer, good performance, and improved conductivity
- Summary
- Abstract
- Description
- Claims
- Application Information
AI Technical Summary
Problems solved by technology
Method used
Image
Examples
Embodiment 1
[0014] (1) Take 0.1g of molybdenum disulfide (MoS 2 ) into the cellulose, magnetically stirred for 10 min, and mixed evenly.
[0015] (2) Ruthenium trichloride (RuCl 3 Containing 37% ruthenium) MoS is added according to the molar ratio of molybdenum to ruthenium metal ions is 20:1 2 In the mixture with cellulose, the coating solution was made after magnetic stirring for 30 min.
[0016] (3) Take an appropriate amount of coating solution to brush the titanium plate on one side. After the coating is uniform, put the titanium plate in an oven at 70°C for 10 minutes, and repeat the above coating process after cooling until the total surface of the coating is obtained. The loading capacity is 1.2 mg / cm 2 , and finally the sample was incubated at an annealing temperature of 500 °C for 1 h to obtain RuO with a molar ratio of molybdenum to ruthenium metal ions of 20:1. 2 -MoO 3 / Ti cathode material.
Embodiment 2
[0018] (1) Take 0.1g of molybdenum disulfide (MoS 2 ) into the cellulose, magnetically stirred for 10 min, and mixed evenly.
[0019] (2) Ruthenium trichloride (RuCl 3 Containing 37% ruthenium) MoS is added according to the molar ratio of molybdenum and ruthenium metal ions to 9:1 2 In the mixture with cellulose, the coating solution was made after magnetic stirring for 30 min.
[0020] (3) Take an appropriate amount of coating solution to brush the titanium plate on one side. After the coating is uniform, put the titanium plate in an oven at 70°C for 10 minutes, and repeat the above coating process after cooling until the total surface of the coating is obtained. The loading capacity is 1.2 mg / cm 2 , and finally the sample was incubated at an annealing temperature of 500 °C for 1 h to obtain RuO with a molar ratio of molybdenum to ruthenium ions of 9:1. 2 -MoO 3 / Ti cathode material.
Embodiment 3
[0022] (1) Take 0.1g of molybdenum disulfide (MoS 2 ) into the cellulose, magnetically stirred for 10 min, and mixed evenly.
[0023] (2) Ruthenium trichloride (RuCl 3 Containing 37% ruthenium) MoS is added according to the molar ratio of molybdenum to ruthenium metal ion molar ratio of 5:5 2 In the mixture with cellulose, the coating solution was made after magnetic stirring for 30 min.
[0024] (3) Take an appropriate amount of coating solution to brush the titanium plate on one side. After the coating is uniform, put the titanium plate in an oven at 70°C for 10 minutes, and repeat the above coating process after cooling until the total surface of the coating is obtained. The loading capacity is 1.2 mg / cm 2 , and finally the sample was incubated at an annealing temperature of 500 °C for 1 h to obtain RuO with a molar ratio of molybdenum to ruthenium ions of 5:5. 2 -MoO 3 / Ti cathode material.
[0025] figure 1 For the RuO that embodiment 1 makes 2 -MoO 3 / Ti cathode...
PUM
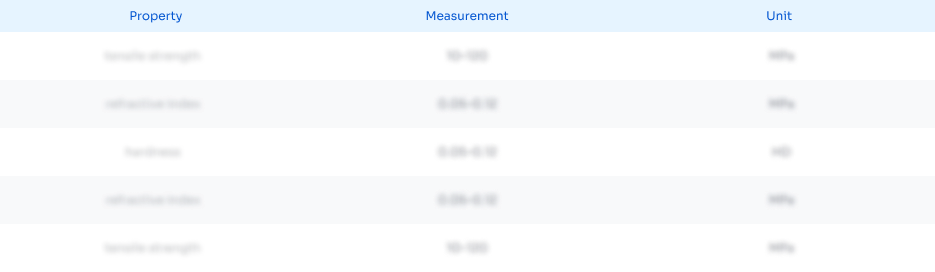
Abstract
Description
Claims
Application Information

- R&D
- Intellectual Property
- Life Sciences
- Materials
- Tech Scout
- Unparalleled Data Quality
- Higher Quality Content
- 60% Fewer Hallucinations
Browse by: Latest US Patents, China's latest patents, Technical Efficacy Thesaurus, Application Domain, Technology Topic, Popular Technical Reports.
© 2025 PatSnap. All rights reserved.Legal|Privacy policy|Modern Slavery Act Transparency Statement|Sitemap|About US| Contact US: help@patsnap.com