Continuous condensation technology of trimethylolpropane and di(trimethylolpropane)
A ditrimethylolpropane and trimethylolpropane technology, which is applied in the continuous condensation process of trimethylolpropane and ditrimethylolpropane, can solve the problems of low output and high added value, and achieve a large production load , high utilization rate of equipment and short average residence time of materials
- Summary
- Abstract
- Description
- Claims
- Application Information
AI Technical Summary
Problems solved by technology
Method used
Image
Examples
Embodiment 1
[0031] Embodiment 1: A kind of continuous condensation process of trimethylolpropane and ditrimethylolpropane.
[0032] Raw material specifications: n-butyraldehyde content 99.5%, formaldehyde content 37%, sodium hydroxide content 32%, water is distilled water.
[0033] Feeding speed: n-butyraldehyde 725 kg / hour, formaldehyde 2386 kg / hour, sodium hydroxide 1500 kg / hour, distilled water 6300 kg / hour.
[0034] The temperature of the continuous reaction heat exchanger is controlled at 35°C, allowing fluctuations of 1°C; the temperature of the continuous reactor is controlled at 40°C, allowing fluctuations of 1°C; the temperature of the continuous neutralization reactor is controlled at 40°C, allowing fluctuations of 1°C ℃; The average residence time of materials in the continuous reaction heat exchanger is 6 minutes, the average residence time of materials in the continuous reactor is 60 minutes, and the average residence time of materials in the continuous neutralization reactor...
Embodiment 2
[0036] Embodiment 2: A continuous condensation process of trimethylolpropane and ditrimethylolpropane.
[0037] Raw material specifications: n-butyraldehyde content 99.5%, formaldehyde content 37%, sodium hydroxide content 32%, water is distilled water.
[0038] Feeding speed: n-butyraldehyde 725 kg / hour, formaldehyde 2435 kg / hour, sodium hydroxide 1500 kg / hour, distilled water 6300 kg / hour.
[0039] The temperature of the continuous reaction heat exchanger is controlled at 35°C, allowing fluctuations of 1°C; the temperature of the continuous reactor is controlled at 50°C, allowing fluctuations of 1°C; the temperature of the continuous neutralization reactor is controlled at 50°C, allowing fluctuations of 1°C °C; the average residence time of the material in the continuous reaction heat exchanger is 6 minutes, the average residence time of the material in the continuous reactor is 45 minutes, and the average residence time of the material in the continuous neutralization react...
Embodiment 3
[0041] Embodiment 3: A continuous condensation process of trimethylolpropane and ditrimethylolpropane.
[0042] Raw material specifications: n-butyraldehyde content 99.5%, formaldehyde content 37%, sodium hydroxide content 32%, water is distilled water.
[0043] Feeding speed: n-butyraldehyde 725 kg / hour, formaldehyde 2597 kg / hour, sodium hydroxide 1500 kg / hour, distilled water 5940 kg / hour.
[0044] The temperature of the continuous reaction heat exchanger is controlled at 35°C, allowing fluctuations of 1°C; the temperature of the continuous reactor is controlled at 55°C, allowing fluctuations of 1°C; the temperature of the continuous neutralization reactor is controlled at 50°C, allowing fluctuations of 1°C ℃; The average residence time of materials in the continuous reaction heat exchanger is 6 minutes, the average residence time of materials in the continuous reactor is 30 minutes, and the average residence time of materials in the continuous neutralization reactor is 10 m...
PUM
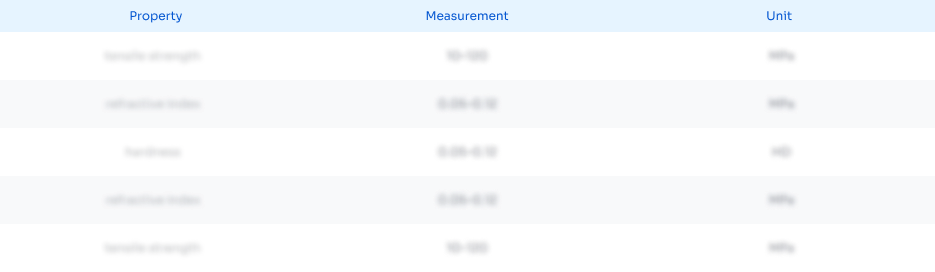
Abstract
Description
Claims
Application Information

- R&D Engineer
- R&D Manager
- IP Professional
- Industry Leading Data Capabilities
- Powerful AI technology
- Patent DNA Extraction
Browse by: Latest US Patents, China's latest patents, Technical Efficacy Thesaurus, Application Domain, Technology Topic, Popular Technical Reports.
© 2024 PatSnap. All rights reserved.Legal|Privacy policy|Modern Slavery Act Transparency Statement|Sitemap|About US| Contact US: help@patsnap.com