Preparation method for compositing dipentaerythritol with tripentearythritol with high yield coefficient
A technology of dipentaerythritol and tripentaerythritol is applied in chemical instruments and methods, ether preparation, organic compound/hydride/coordination complex catalyst, etc., and can solve the problems of difficult separation, complicated production process, complicated operation, etc. The effect of improving reaction conditions, simple and easy separation, and high product purity
- Summary
- Abstract
- Description
- Claims
- Application Information
AI Technical Summary
Problems solved by technology
Method used
Image
Examples
Embodiment 1
[0049] Carry out pretreatment to the styrene copolymerized cross-linked structure macromolecular matrix loaded with quaternary amine groups, take 8g of potassium hydroxide and configure it into a 4wt% alkaline solution, and 50g of the polymer-supported solid alkali catalyst sieved with a 100-mesh standard sieve Add it to the above alkaline solution, stir it evenly, put it into a silica gel column, then soak it overnight in the air at room temperature, filter it with 2 times the volume of distilled water to remove metal ions and other impurities, and dry it at 50°C to obtain the treated solid base catalyst.
[0050] Add 5 g of the above-mentioned treated solid base catalyst, 20 g of monopentaerythritol and 80 g of water into a reaction kettle with a stirrer, and place it in a water bath at 20-40 °C; add 36.2 g of 37% formaldehyde and 12.0 g of 40% acetaldehyde Mix and stir for 30 minutes; prepare 90ml of 6% KOH solution, heat the temperature of the water bath to 40°C under stir...
Embodiment 2
[0053] Add 5 g of the above-mentioned treated solid base catalyst, 20 g of monopentaerythritol and 80 g of water into a reaction kettle with a stirrer, and place it in a water bath at 20° C.; mix and stir 36.5 g of 37% formaldehyde and 13.2 g of 40% acetaldehyde 30min; prepare 90ml of 4% KOH solution, heat the temperature of the water bath to 40°C under stirring, then continuously and evenly add the prepared KOH solution, formaldehyde, and acetaldehyde mixture into the reaction kettle, and drop it for 60 minutes , the mixture of formaldehyde and acetaldehyde is completely dripped, and 2 / 5 of the KOH solution is left. Adjust the temperature of the water bath to 50°C, speed up the rate of KOH solution addition, and continue the dropwise addition for 30 minutes. After the addition of the KOH solution, continue the reaction for 2 hours. Same as Example 1, the results are shown in Table 1.
Embodiment 3
[0055] Add 5 g of the above-mentioned treated solid base catalyst, 20 g of monopentaerythritol and 80 g of water into a reaction kettle with a stirrer, and place it in a water bath at 20-40 °C; add 36.3 g of 37% formaldehyde and 12.9 g of 40% acetaldehyde Mix and stir for 30 minutes; configure 90ml of 2% KOH solution, heat the water bath temperature to 40°C under stirring, then continuously and evenly add the prepared KOH solution, formaldehyde and acetaldehyde mixture into the reaction kettle, drop After 60 minutes, the mixture of formaldehyde and acetaldehyde was completely dripped, and 2 / 5 of the KOH solution remained. Adjust the temperature of the water bath to 50°C, speed up the rate of KOH solution dropwise, and continue to add dropwise for 30 minutes. After the dropwise addition of KOH solution, continue to react for 2 hours. Same as Example 1, the results are shown in Table 1.
PUM
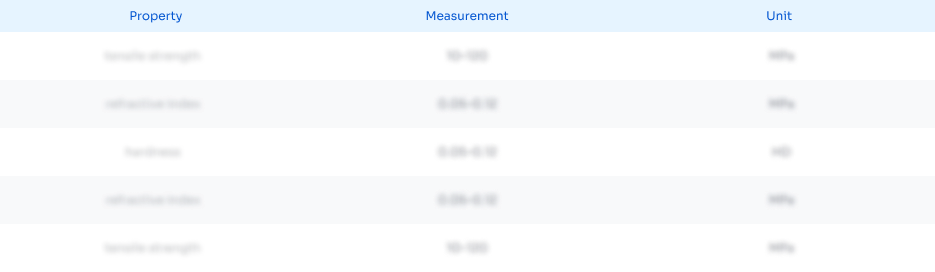
Abstract
Description
Claims
Application Information

- R&D Engineer
- R&D Manager
- IP Professional
- Industry Leading Data Capabilities
- Powerful AI technology
- Patent DNA Extraction
Browse by: Latest US Patents, China's latest patents, Technical Efficacy Thesaurus, Application Domain, Technology Topic, Popular Technical Reports.
© 2024 PatSnap. All rights reserved.Legal|Privacy policy|Modern Slavery Act Transparency Statement|Sitemap|About US| Contact US: help@patsnap.com