Granulation system for organic composite material master batch
A composite material and masterbatch technology, applied in the direction of coating, etc., can solve problems such as low degree of production automation, inability to accurately control reaction extrusion, and substandard extrusion equipment, and achieve strong distribution mixing and dispersion mixing capabilities, which is beneficial to Effect of mixing, increasing shear stress and shear rate
- Summary
- Abstract
- Description
- Claims
- Application Information
AI Technical Summary
Problems solved by technology
Method used
Image
Examples
Embodiment
[0033] Please refer to figure 1 , The granulation system of the organic composite material masterbatch of the present invention includes: a mixing device 100, an extruding device 200, a cooling device 300, a material cutting device 400, a conveying device 500 and a packaging device 600 connected in sequence.
[0034] Please refer to figure 1 and 2, the mixing device 100 includes: a material control chamber 110, a metering chamber 120, a mixing storage room 130 and a control room 140 communicated in sequence from top to bottom, and the control room 140 is connected to the material control room 110, the metering room 120 and the mixing storage room respectively. The material chamber 130 and the control chamber 140 are used to control the feed rate of the material control chamber 110 , control the addition of the metering chamber 120 , and control the stirring speed and feeding speed of the mixing storage chamber 130 .
[0035] A plurality of material control bins 113 are arran...
PUM
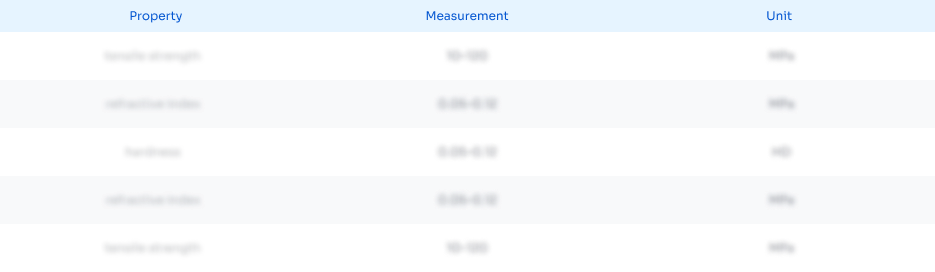
Abstract
Description
Claims
Application Information

- R&D
- Intellectual Property
- Life Sciences
- Materials
- Tech Scout
- Unparalleled Data Quality
- Higher Quality Content
- 60% Fewer Hallucinations
Browse by: Latest US Patents, China's latest patents, Technical Efficacy Thesaurus, Application Domain, Technology Topic, Popular Technical Reports.
© 2025 PatSnap. All rights reserved.Legal|Privacy policy|Modern Slavery Act Transparency Statement|Sitemap|About US| Contact US: help@patsnap.com