A kind of processing technology of backstop spare parts of heavy-duty bearing of railway wagon
A railway freight car and processing technology technology, applied in the field of bearing processing, can solve the problems of limiting the surface accuracy requirements of the two ends of the parts, the processing cost of product bumps, and the backward processing technology, so as to solve the problems of poor versatility, improve production efficiency and resource utilization. reasonable effect
- Summary
- Abstract
- Description
- Claims
- Application Information
AI Technical Summary
Problems solved by technology
Method used
Image
Examples
Embodiment 1
[0044] A processing technology for backstop parts of heavy-duty bearings of railway wagons, comprising the following steps:
[0045] (1) Select the bearing backstop forging, and use a lathe to sequentially process the forging end face 1, the first inner hole 2, and the safety angle 3;
[0046] The number of safety corners 3 completed in (1) is 2. After the processing is completed, as follows: figure 1 As shown, the first stage;
[0047] (2) Turn the forging 180 degrees clockwise, and use a lathe to sequentially process the end face 1-1, outer diameter 4, and safety angle 3 of the forging;
[0048] The number of safety corners 3 completed in (2) is 2. After the processing is completed, as follows: figure 2 As shown, the second stage;
[0049] The lathe described in the above steps (1) and (2) adopts the C7232 hydraulic profiling lathe;
[0050] (3) Carry out turning on the end face 1-2 of the forging, the slope of the large diameter 5, and the fillet 6 of the large diamete...
Embodiment 2
[0055] A processing technology for the rear gear parts of heavy-duty bearings of railway wagons, the process is divided into 14 processes, and the specific steps are as follows:
[0056] a. Select the forging of the bearing backstop, use a lathe to process the end face of the forging in turn, rough turn the first inner hole, turn the safety corner, and complete the process 1, such as Figure 11 Shown; Among them, C7232 and CD7632 lathes are used;
[0057] b. Rough car outer surface, car end face, car safety corner, complete process 2, such as Figure 12 Shown; Among them, C7232 and CD7632 lathes are used;
[0058] c, soft grinding, complete process 3, such as Figure 13 Shown; where M7475B surface grinder is used;
[0059] d. The boss outside the car, the rounded corners of the boss outside the car, complete the process 4, such as Figure 14 Shown; Wherein adopt C7632, CD7632 lathe;
[0060] e. Rough car large inner hole, complete process 5, such as Figure 15 Shown; Whe...
PUM
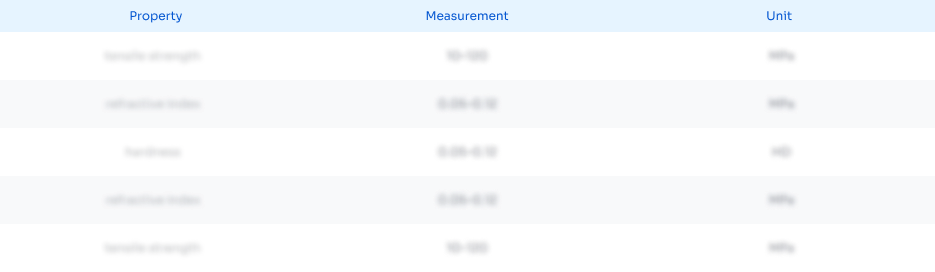
Abstract
Description
Claims
Application Information

- R&D
- Intellectual Property
- Life Sciences
- Materials
- Tech Scout
- Unparalleled Data Quality
- Higher Quality Content
- 60% Fewer Hallucinations
Browse by: Latest US Patents, China's latest patents, Technical Efficacy Thesaurus, Application Domain, Technology Topic, Popular Technical Reports.
© 2025 PatSnap. All rights reserved.Legal|Privacy policy|Modern Slavery Act Transparency Statement|Sitemap|About US| Contact US: help@patsnap.com