Device and device for measuring gravity center parameters of helicopter rotor blades
A helicopter rotor and parameter measurement technology, applied in the direction of measuring devices, machine/structural component testing, static/dynamic balance testing, etc., can solve problems such as cumbersome methods, influence of helicopter blade quality, inability to measure chord-wise center of gravity parameters, etc. , to achieve the effect of uniform blade quality
- Summary
- Abstract
- Description
- Claims
- Application Information
AI Technical Summary
Problems solved by technology
Method used
Image
Examples
specific Embodiment approach 1
[0023] Specific implementation mode 1: Combination Figure 1 ~ Figure 3 Detailed description The device for measuring the center of gravity parameter of a helicopter rotor blade in this embodiment specifically includes two parts: a blade center of gravity parameter measurement subsystem 1 and a mass sensor standard stator system 2; the blade center of gravity parameter measurement subsystem 1 includes the helicopter blade center of gravity. Parameter measurement test bench 1-1, the first high-precision quality sensor 1-2-1, the second high-precision quality sensor 1-2-2, the third high-precision quality sensor 1-2-3, and the signal acquisition device 1-3 , High-speed data processor 1-4 and micro-control computer 1-5; Helicopter rotor blade center of gravity measurement test bench 1-1 is used to place and adjust the level of the reference blade 1-6, helicopter rotor blade center of gravity measurement test bench 1-1 is a T-shaped frame composed of a main board 1-1-3 and two wing...
specific Embodiment approach 2
[0024] Specific embodiment two: the helicopter rotor blade gravity center parameter measurement device in this embodiment includes a mass sensor calibration device 2-1, three high-precision mass sensors 2-2, a standard weight 2-3, and a HBMQUANTUMX signal acquisition device 2-4 , High-speed data processor and optimization algorithm 2-5 and micro-control computer 2-6; the mass sensor calibration device 2-1 is a tripod, one side of the tripod is used to place and fix the standard weight 2-3 and its relative angle To fix the high-precision quality sensor 2-2 to be calibrated, the HBMQUANTUMX signal acquisition device 2-4 is used to collect the signal of the calibrated high-precision quality sensor 2-2, and the high-speed data processor 2-5 is used to calculate the high-precision quality sensor in real time. 2-2 signal data, the micro control computer 2-6 is used to display the calibration results of the high-precision quality sensor 2-2.
specific Embodiment approach 3
[0025] Specific embodiment three: The measurement method of the parameters of the center of gravity of a helicopter rotor blade using the devices in the first embodiment and the second embodiment is specifically as follows:
[0026] Step 1. Mass sensor calibration: Place and fix the standard weight 2-3 and the high-precision mass sensor 2-2 to be calibrated on the mass sensor calibration device 2-1 as image 3 As shown, the HBMQUANTUMX signal acquisition device 2-4 collects the signal of the calibrated high-precision quality sensor 2-2, then uses the high-speed data processor 2-5 to calculate the quality sensor to be calibrated, and displays the calibration results on the micro-control computer 2-6 .
[0027] Step 2: Measurement of the parameters of the center of gravity of the helicopter rotor blades: The test bench for the measurement of the center of gravity parameters of the entire helicopter blade is horizontal, and the first high-precision mass sensor 1-2-1 and the second high...
PUM
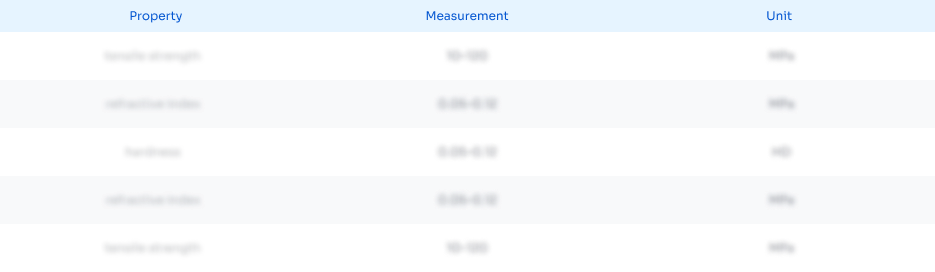
Abstract
Description
Claims
Application Information

- Generate Ideas
- Intellectual Property
- Life Sciences
- Materials
- Tech Scout
- Unparalleled Data Quality
- Higher Quality Content
- 60% Fewer Hallucinations
Browse by: Latest US Patents, China's latest patents, Technical Efficacy Thesaurus, Application Domain, Technology Topic, Popular Technical Reports.
© 2025 PatSnap. All rights reserved.Legal|Privacy policy|Modern Slavery Act Transparency Statement|Sitemap|About US| Contact US: help@patsnap.com