A kind of twist drill for hole processing of laminated welded steel
A hole processing and twist drilling technology, which is applied in twist drills, metal processing equipment, drilling/drilling equipment, etc., can solve the problem of the sharpness of the peripheral cutting edge, the deviation of the drill bit and the opening of the hole, which affect the self-centering ability of the drill tip. The burr is too large, which affects the service life of the drill bit, etc., so as to reduce the occurrence rate of the burr at the hole, make it easier to drill into the workpiece, and reduce the effect of centering instability
- Summary
- Abstract
- Description
- Claims
- Application Information
AI Technical Summary
Problems solved by technology
Method used
Image
Examples
Embodiment 1
[0032] Such as Figure 1 to Figure 6 As shown, the twist drill used for hole processing of laminated welded steel in this embodiment includes a cutting part and a shank 1, the cutting part includes a drill point 2 and a secondary cutting part 3, and the drill point 2 is provided with two main cutting edges 21 and the chisel edge 22 connecting the two main cutting edges 21, the secondary cutting part 3 is provided with two flutes 31 and two first lands 32, the first lands 32 intersect with the flutes 31 to form a secondary cutting The edge 33 and the secondary cutting portion 3 are composed of two blades 30 , the first land 32 is provided on the blade 30 , and the first land 32 is provided with a peripheral edge 321 , the peripheral edge 321 intersects with the secondary cutting edge 33 . The main cutting edge 21 is provided with a negative chamfer 4, and the negative chamfer 4 does not pass through the intersection of the main cutting edge 21 and the chisel edge 22. The length...
Embodiment 2
[0043] Such as Figure 7 As shown, the twist drill used for hole processing of stacked welded steel products in this embodiment is basically the same as that in Embodiment 1, the only difference is that:
[0044] In this embodiment, the negative chamfer 4 on the main cutting edge 21 is replaced by a honing surface 5, and the honing surface 5 is an outwardly convex arc surface. The honing surface 5 can also strengthen the drill tip, and the value of the rake angle γ1 of the honing surface 5 is the angle between the line connecting the two starting points of the arc and the axis.
[0045] The rest are the same as in Embodiment 1, and will not be repeated here.
PUM
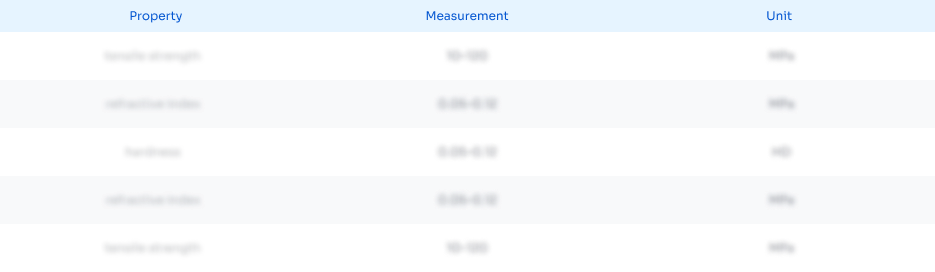
Abstract
Description
Claims
Application Information

- Generate Ideas
- Intellectual Property
- Life Sciences
- Materials
- Tech Scout
- Unparalleled Data Quality
- Higher Quality Content
- 60% Fewer Hallucinations
Browse by: Latest US Patents, China's latest patents, Technical Efficacy Thesaurus, Application Domain, Technology Topic, Popular Technical Reports.
© 2025 PatSnap. All rights reserved.Legal|Privacy policy|Modern Slavery Act Transparency Statement|Sitemap|About US| Contact US: help@patsnap.com